Method for preparing iron powder through red mud suspension roasting
A technology of suspension roasting and iron concentrate powder, which is applied in the field of mineral processing, can solve the problems of inability to realize resource utilization of red mud, inability to effectively separate alumina and iron minerals, and low separation efficiency
- Summary
- Abstract
- Description
- Claims
- Application Information
AI Technical Summary
Problems solved by technology
Method used
Image
Examples
Embodiment 1
[0027] The iron grade TFe of red mud is 26%, containing Al by weight percentage 2 o 3 18%, SiO 2 11%, Na 2 O 1.2%;
[0028] Process such as figure 1 shown;
[0029] Grind the red mud until the particle size -200 mesh accounts for 65% of the total weight to obtain red mud ore powder; subject the red mud ore powder to a stage of weak magnetic separation with a magnetic field strength of 600Oe to obtain a stage of weak magnetic separation concentrate and a stage of Weak magnetic separation tailings;
[0030] A section of weak magnetic separation tailings is subjected to strong magnetic separation with a magnetic field strength of 6000Oe to obtain strong magnetic separation concentrate and strong magnetic separation tailings; a section of weak magnetic separation concentrate and strong magnetic separation concentrate are mixed as pre-enrichment concentrate mine;
[0031] Put the pre-enriched concentrate in the oxidation roasting furnace, feed gas and air to keep the pre-e...
Embodiment 2
[0036] The iron grade TFe of red mud is 47%, containing Al by weight percentage 2 o 3 13%, SiO 2 3%, Na 2 O 0.5%;
[0037] Method is with embodiment 1, and difference is:
[0038] (1) Grinding the red mud to a particle size of -200 mesh accounts for 60% of the total weight, and the magnetic field strength of a section of weak magnetic separation is 1000Oe;
[0039] (2) The magnetic field intensity of strong magnetic separation is 8000Oe;
[0040] (3) The temperature of oxidation roasting is 950℃, the time is 5min, and the flow rate of gas and air is 25m per ton of pre-enriched concentrate. 3 / h;
[0041] (4) The temperature of reduction roasting is 750°C, the time is 2min, and the reducing gas is H 2 , the flow rate of reducing gas is H 2 The total amount is 15m 3 / h; the ratio of nitrogen and reducing gas is 3:1;
[0042] (5) Grinding the roasted ore until the particle size-400 mesh accounts for 60% of the total weight, the magnetic field strength of the second stag...
Embodiment 3
[0044] The iron grade TFe of red mud is 38%, containing Al by weight percentage 2 o 3 15%, SiO 2 9%, Na 2 O 0.9%;
[0045] Method is with embodiment 1, and difference is:
[0046] (1) Grinding the red mud to a particle size of -200 mesh accounts for 70% of the total weight, and the magnetic field strength of a section of weak magnetic separation is 1500Oe;
[0047] (2) The magnetic field intensity of strong magnetic separation is 9000Oe;
[0048] (3) The temperature of oxidative roasting is 850°C and the time is 15min, and the flow rate of gas and air is 15m per ton of pre-enriched concentrate. 3 / h;
[0049] (4) The temperature of reduction roasting is 550°C, the time is 8min, the reduction gas is coal gas, and the flow rate of reduction gas is based on the amount of CO and H introduced per ton of oxidized ore powder. 2 The total amount is 10m 3 / h; the ratio of nitrogen and reducing gas is 4:1;
[0050] (5) Grinding the roasted ore until the particle size-400 mesh...
PUM
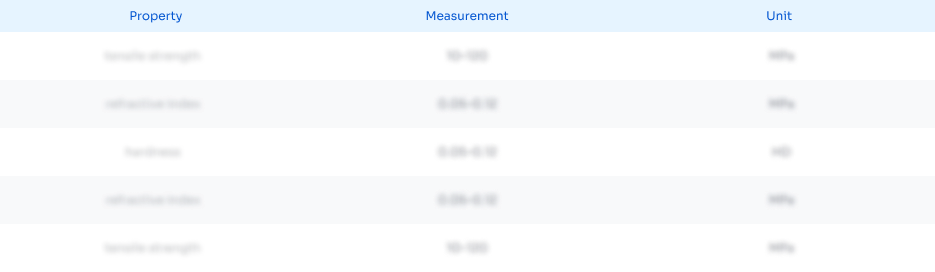
Abstract
Description
Claims
Application Information

- R&D
- Intellectual Property
- Life Sciences
- Materials
- Tech Scout
- Unparalleled Data Quality
- Higher Quality Content
- 60% Fewer Hallucinations
Browse by: Latest US Patents, China's latest patents, Technical Efficacy Thesaurus, Application Domain, Technology Topic, Popular Technical Reports.
© 2025 PatSnap. All rights reserved.Legal|Privacy policy|Modern Slavery Act Transparency Statement|Sitemap|About US| Contact US: help@patsnap.com