Large plastic shape and deformation blank-making method for eliminating anisotropy of magnesium alloy bar material with large height-diameter ratio
An anisotropic and plastic deformation technology, applied in the direction of manufacturing tools, metal processing equipment, metal extrusion dies, etc., can solve problems such as unevenness, difficulty in large deformation, overall performance of uneven components, etc., to achieve uniformity enhancement, Significant economic benefits and the effect of eliminating anisotropy
- Summary
- Abstract
- Description
- Claims
- Application Information
AI Technical Summary
Problems solved by technology
Method used
Image
Examples
Embodiment Construction
[0019] In order to make the objectives, technical solutions and advantages of the present invention clearer, the present invention will be further described in detail below in conjunction with specific embodiments. It should be understood that the specific embodiments described herein are only used to explain the present invention, and not to limit the present invention.
[0020] See figure 1 , Figure 4 , Upsetting die 1, mainly includes upsetting punch 11 and upsetting die 12, where the middle convex portion 112 of the bottom end 111 of the upsetting punch 11 is a parabola, and the equation is y=0.005x 2 , The two ends of side 113 are symmetrical involutes, the equation is x(t)=8*(cos(t)+t*sin(t)), y(t)=8*(sin(t)-t* cos(t)). At the beginning of upsetting, the middle convex portion 112 first contacts the middle of the blank to deform the blank in the center area of the end of the blank first. Compared with the traditional upsetting deformation, this area is changed to the non-...
PUM
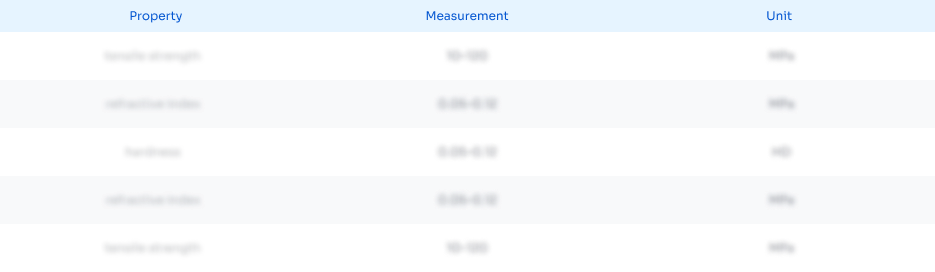
Abstract
Description
Claims
Application Information

- Generate Ideas
- Intellectual Property
- Life Sciences
- Materials
- Tech Scout
- Unparalleled Data Quality
- Higher Quality Content
- 60% Fewer Hallucinations
Browse by: Latest US Patents, China's latest patents, Technical Efficacy Thesaurus, Application Domain, Technology Topic, Popular Technical Reports.
© 2025 PatSnap. All rights reserved.Legal|Privacy policy|Modern Slavery Act Transparency Statement|Sitemap|About US| Contact US: help@patsnap.com