Hybrid electromagnetic induction and laser heating stamping method and device
A technology of electromagnetic induction heating and laser heating, which is applied in metal processing equipment, forming tools, manufacturing tools, etc., can solve the problems of shortened mold fatigue life, poor forming ability, and easy fracture in large deformation areas, so as to reduce production costs and The effect of technical threshold, increasing production capacity and mold life, and reducing hardware capital investment
- Summary
- Abstract
- Description
- Claims
- Application Information
AI Technical Summary
Problems solved by technology
Method used
Image
Examples
Embodiment Construction
[0023] The present invention will be further described below in conjunction with the accompanying drawings and specific embodiments, so that those skilled in the art can better understand the present invention and implement it, but the examples given are not intended to limit the present invention.
[0024] The invention provides a hybrid electromagnetic induction and laser heating stamping method and its device. In the method, the electromagnetic induction method is used to heat the sheet metal to a temperature at which the microstructure of the material does not change, and then the laser is used to rapidly irradiate and heat the area requiring large deformation. , and then improve the flow capacity of this area, and then use conventional stamping methods for deep drawing, bending, punching, embossing and other forming processes. In this way, complex geometric features can be formed, the stamping force can be reduced and the life of the die can be extended. The present inven...
PUM
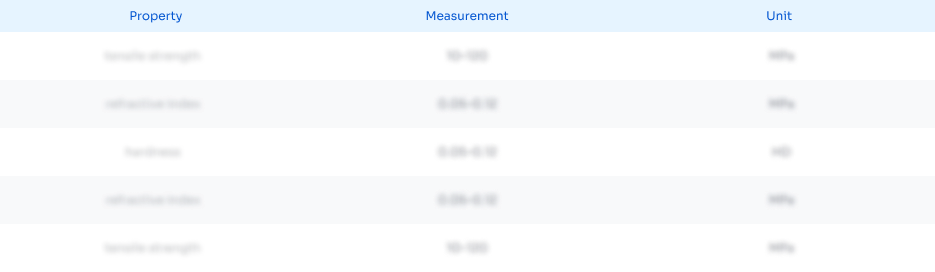
Abstract
Description
Claims
Application Information

- R&D Engineer
- R&D Manager
- IP Professional
- Industry Leading Data Capabilities
- Powerful AI technology
- Patent DNA Extraction
Browse by: Latest US Patents, China's latest patents, Technical Efficacy Thesaurus, Application Domain, Technology Topic, Popular Technical Reports.
© 2024 PatSnap. All rights reserved.Legal|Privacy policy|Modern Slavery Act Transparency Statement|Sitemap|About US| Contact US: help@patsnap.com