Polyester grouting material and preparation method thereof
A grouting material and polyester technology, applied in the field of polyester grouting material and its preparation, can solve the problems of unfavorable wide application of polyester grouting material and the like
- Summary
- Abstract
- Description
- Claims
- Application Information
AI Technical Summary
Problems solved by technology
Method used
Image
Examples
preparation example Construction
[0069] The preparation method of the polyester grouting material of an embodiment, comprises the steps:
[0070] S10, providing the above-mentioned first mixing component, second mixing component and third mixing component.
[0071] S20. Mix the first mixing component and the second mixing component uniformly, then add the third mixing component and mix uniformly to obtain polyester grout.
[0072] In the process of uniformly mixing the first mixing component and the second mixing component, each component in the first mixing component and the second mixing component reacts to form a cross-linked network structure.
[0073] Preferably, before the first mixing component and the second mixing component are completely cross-linked, the third mixing component is added in batches and mixed evenly, and then the pouring construction is performed.
Embodiment 2
[0084] The preparation method of the polyester grout of embodiment 2 comprises the steps:
[0085] Mix E51 type epoxy resin, KH550 coupling agent, n-butyl glycidyl ether, polyamide (amine value 320-480) and DMP-30 quickly and evenly. Within 5 minutes, add the third mixing component consisting of sand, barium sulfate powder, fly ash and talcum powder in batches, stir and mix evenly to obtain grouting material.
[0086] When the polyester grout of Example 2 is poured into the underwater molding (28 days) at 10°C, the compressive strength of the sample is 68.2MPa; the normal tensile strength of the underwater and C30 concrete is 2.7MPa, which is the cohesion of the concrete at the bonding place Destruction; shrinkage rate 0.1%; polyester grouting material has no obvious dispersion in water, and has excellent flowability.
[0087] Please also see figure 1 and figure 2 , before using the polyester grout of Example 2 for underwater pouring, the gap on the concrete surface was ab...
PUM
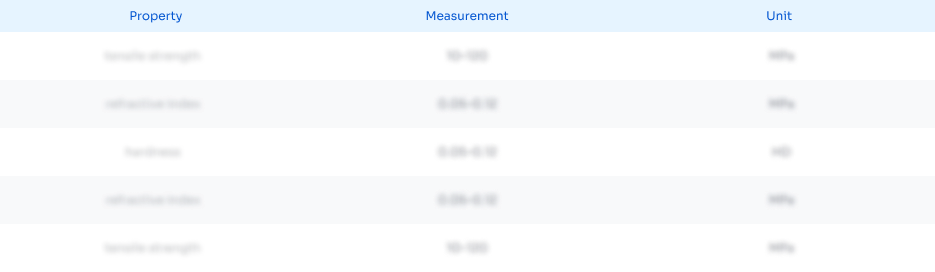
Abstract
Description
Claims
Application Information

- R&D Engineer
- R&D Manager
- IP Professional
- Industry Leading Data Capabilities
- Powerful AI technology
- Patent DNA Extraction
Browse by: Latest US Patents, China's latest patents, Technical Efficacy Thesaurus, Application Domain, Technology Topic, Popular Technical Reports.
© 2024 PatSnap. All rights reserved.Legal|Privacy policy|Modern Slavery Act Transparency Statement|Sitemap|About US| Contact US: help@patsnap.com