A model predictive torque control method for built-in permanent magnet synchronous motor
A permanent magnet synchronous motor and synchronous motor technology, applied in motor generator control, electronic commutation motor control, control system, etc., can solve the problems of poor motor dynamic response torque control effect and cumbersome coefficient selection.
- Summary
- Abstract
- Description
- Claims
- Application Information
AI Technical Summary
Problems solved by technology
Method used
Image
Examples
Embodiment Construction
[0060] A model predictive torque control method for an interior permanent magnet synchronous motor of the present invention will be described in detail below in conjunction with the embodiments and the accompanying drawings.
[0061] A built-in permanent magnet synchronous motor model predictive torque control method of the present invention is used for figure 1 The control method of the built-in permanent magnet synchronous motor control system shown, such as figure 2 , image 3 , Figure 4 shown, including the following steps:
[0062] 1) Collect the voltage, current and speed signals at the beginning of the kth control cycle of the built-in permanent magnet synchronous motor, and perform coordinate transformation; including:
[0063] Collect the inverter DC bus voltage u at the beginning of the kth control cycle through the analog-to-digital conversion (A / D) interface inside the microprocessor (DSP) on the main control board dc (k) and three-phase stator current i a (...
PUM
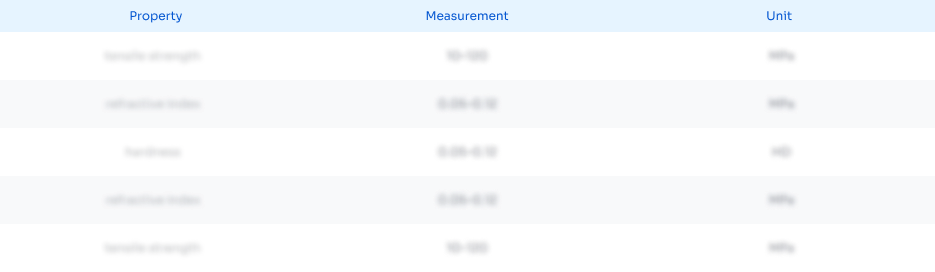
Abstract
Description
Claims
Application Information

- Generate Ideas
- Intellectual Property
- Life Sciences
- Materials
- Tech Scout
- Unparalleled Data Quality
- Higher Quality Content
- 60% Fewer Hallucinations
Browse by: Latest US Patents, China's latest patents, Technical Efficacy Thesaurus, Application Domain, Technology Topic, Popular Technical Reports.
© 2025 PatSnap. All rights reserved.Legal|Privacy policy|Modern Slavery Act Transparency Statement|Sitemap|About US| Contact US: help@patsnap.com