High-plasticity aluminum alloy processing technology
A processing technology and aluminum alloy technology, which is applied in the field of high plasticity aluminum alloy processing technology, can solve the problems of low plasticity, shrinkage, and incomplete degassing and purification of aluminum-silicon alloy materials, so as to meet service requirements, improve plasticity, and crystallization. grainy effect
- Summary
- Abstract
- Description
- Claims
- Application Information
AI Technical Summary
Problems solved by technology
Method used
Image
Examples
Embodiment 1
[0014] A high plasticity aluminum alloy processing technology, the method comprises the following steps:
[0015] Step 1. Use 39 parts of Al, 13 parts of Si, 1.4 parts of Cu, 2.6 parts of Zn, 2 parts of Fe, and 0.6 parts of Sr as smelting materials, put Al, Zn and Si into the smelting furnace, heat to 780 ° C, and make it Melt into a melt, then add Cu, Fe and Sr to the melt with a gas carrier, keep stirring at a constant temperature for 10 minutes, then adjust the temperature to 750 ° C, blow argon into the melting furnace to refine the mixed melt for 16 minutes, and remove Scum on the liquid surface to obtain a mixed melt;
[0016] Step 2. Send the mixed melt into the intermediate frequency furnace, raise the temperature to 1200°C in an environment filled with nitrogen, and add 3.4 parts of TiO 2 -ZrO 2 Composite metal powder and 1.7 parts of Pb, keep stirring at constant temperature for 8 minutes, then send the material into the injection molding equipment, adjust the temp...
Embodiment 2
[0023] 27 parts of Al, 11 parts of Si, 1.4 parts of Cu, 2.6 parts of Zn, 2 parts of Fe, and 0.6 parts of Sr are used as melting materials, and Al, Zn and Si are put into the melting furnace, heated to 780 ° C, and melted into molten Then add Cu, Fe and Sr to the melt with a gas carrier, keep stirring at a constant temperature for 10 minutes, then adjust the temperature to 750°C, blow argon into the melting furnace to refine the mixed melt for 16 minutes, and remove the liquid floating Slag, obtain mixed melt; All the other steps are identical with embodiment 1.
Embodiment 3
[0025] 33 parts of Al, 14 parts of Si, 1.4 parts of Cu, 2.6 parts of Zn, 2 parts of Fe, and 0.6 parts of Sr are used as melting materials, and Al, Zn and Si are put into the melting furnace, heated to 780 ° C, and melted into molten Then add Cu, Fe and Sr to the melt with a gas carrier, keep stirring at a constant temperature for 10 minutes, then adjust the temperature to 750°C, blow argon into the melting furnace to refine the mixed melt for 16 minutes, and remove the liquid floating Slag, obtain mixed melt; All the other steps are identical with embodiment 1.
PUM
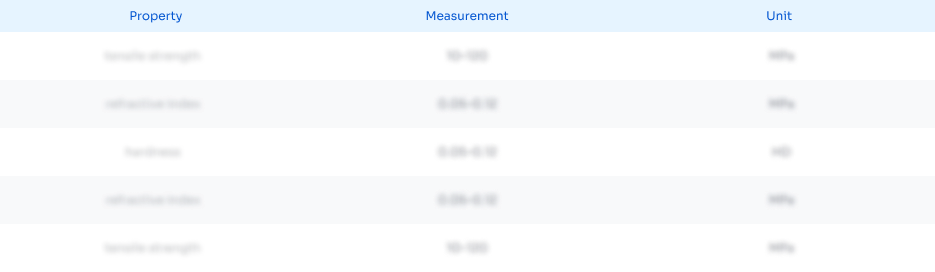
Abstract
Description
Claims
Application Information

- R&D
- Intellectual Property
- Life Sciences
- Materials
- Tech Scout
- Unparalleled Data Quality
- Higher Quality Content
- 60% Fewer Hallucinations
Browse by: Latest US Patents, China's latest patents, Technical Efficacy Thesaurus, Application Domain, Technology Topic, Popular Technical Reports.
© 2025 PatSnap. All rights reserved.Legal|Privacy policy|Modern Slavery Act Transparency Statement|Sitemap|About US| Contact US: help@patsnap.com