Foaming process of water-borne polyurethane foam for finished automobile
A water-based polyurethane and foam technology, which is applied in the equipment field of automotive materials, can solve the problems of insufficient shockproof, heat insulation, sound insulation, low comfort in the car, and travel discomfort, and achieves good thermal insulation effect and adhesion performance. Strong and hygroscopic effect
- Summary
- Abstract
- Description
- Claims
- Application Information
AI Technical Summary
Problems solved by technology
Method used
Examples
specific Embodiment 1
[0020] A foaming process of water-based polyurethane vehicle foam, the foaming process steps are:
[0021] (1) The components and proportions of the water-based polyurethane foam are: 40 parts of water-based polyether polyol, 41 parts of dichlorohydrogen ester, 8 parts of whisker silicon, and 5 parts of glass fiber;
[0022] (2) fully mix and stir each component of the water-based polyurethane foam in step 1 according to the required ratio, and then extrude and granulate through an extruder;
[0023] (3) Then place the extruded material in the extrusion granulator into the prepared foaming abrasive for foaming treatment, and then place the foamed sponge foam at a specified distance for aging treatment, and then Take out after cooling down.
[0024] Further, the foaming room temperature is controlled at 0-25°C during the foaming.
[0025] Further, the material temperature of the water-based polyurethane foam is controlled at 21-23° C., and the foaming time of the material is ...
specific Embodiment 2
[0031] A foaming process of water-based polyurethane vehicle foam, the foaming process steps are:
[0032] (1) The components and proportions of the water-based polyurethane foam are: 40-41 parts of water-based polyether polyol, 42 parts of dichlorohydrogen ester, 9 parts of whisker silicon, and 3 parts of glass fiber;
[0033] (2) fully mix and stir each component of the water-based polyurethane foam in step 1 according to the required ratio, and then extrude and granulate through an extruder;
[0034] (3) Then place the extruded material in the extrusion granulator into the prepared foaming abrasive for foaming treatment, and then place the foamed sponge foam at a specified distance for aging treatment, and then Take out after cooling down.
[0035] Further, the foaming room temperature is controlled at 0-28°C during the foaming.
[0036] Further, the material temperature of the water-based polyurethane foam is controlled at 24-26° C., and the foaming time of the material ...
PUM
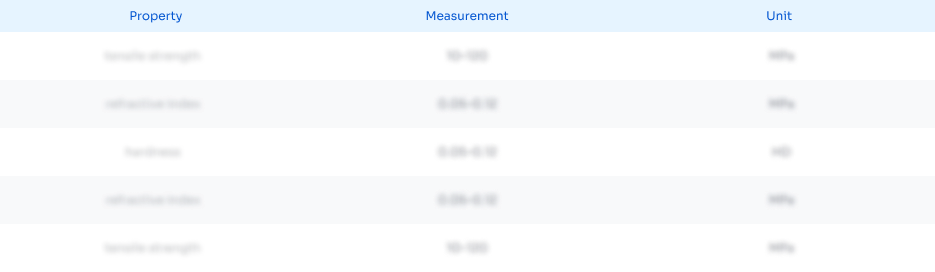
Abstract
Description
Claims
Application Information

- Generate Ideas
- Intellectual Property
- Life Sciences
- Materials
- Tech Scout
- Unparalleled Data Quality
- Higher Quality Content
- 60% Fewer Hallucinations
Browse by: Latest US Patents, China's latest patents, Technical Efficacy Thesaurus, Application Domain, Technology Topic, Popular Technical Reports.
© 2025 PatSnap. All rights reserved.Legal|Privacy policy|Modern Slavery Act Transparency Statement|Sitemap|About US| Contact US: help@patsnap.com