Real-time monitoring method of state of cutting tool for numerical control machining of complicated structural component based on deep learning
A deep learning and complex structure technology, applied in neural learning methods, manufacturing tools, metal processing equipment, etc., can solve problems such as poor adaptability of parts, heavy monitoring and learning workload, poor model generalization ability, etc., to achieve a wide range of applications, The effect of shortening the production cycle and reducing the production cost
- Summary
- Abstract
- Description
- Claims
- Application Information
AI Technical Summary
Problems solved by technology
Method used
Image
Examples
Embodiment Construction
[0029] The following structural drawings and embodiments further illustrate the present invention.
[0030] A deep learning-based real-time monitoring method for the tool status of CNC machining of complex structural parts, such as figure 1As shown, it includes the following specific steps as follows:
[0031] Step 1: Establish a training sample database; select typical sensor signal data, discretely store each type of signal data, and affix corresponding tool status labels as training samples;
[0032] Step 2: Construction and training of deep learning model; construct deep confidence network, input original signal data, output signal feature extraction results, use unlabeled training set samples to train network; construct convolutional neural network, input monitoring information matrix, output tool State identification results, using labeled training set samples to train the network;
[0033] Step 3: NC machining tool status monitoring; during NC machining, monitor the s...
PUM
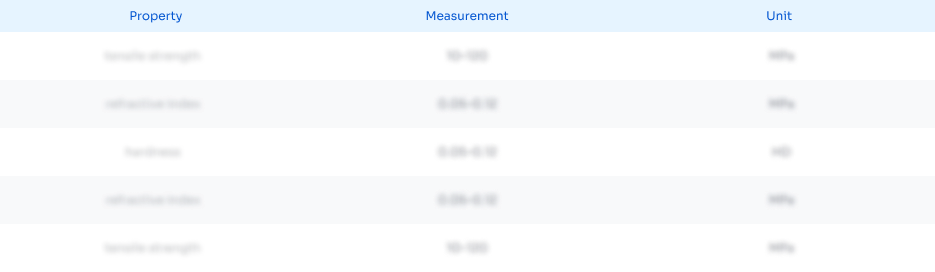
Abstract
Description
Claims
Application Information

- R&D
- Intellectual Property
- Life Sciences
- Materials
- Tech Scout
- Unparalleled Data Quality
- Higher Quality Content
- 60% Fewer Hallucinations
Browse by: Latest US Patents, China's latest patents, Technical Efficacy Thesaurus, Application Domain, Technology Topic, Popular Technical Reports.
© 2025 PatSnap. All rights reserved.Legal|Privacy policy|Modern Slavery Act Transparency Statement|Sitemap|About US| Contact US: help@patsnap.com