Process of producing novel environment-friendly TPU (thermoplastic polyurethane) awning
A kind of tarpaulin and environmental protection technology, applied in the direction of final product manufacturing, sustainable manufacturing/processing, textile/flexible product manufacturing, etc., can solve the problems of easy residual small bubble thickness, easy degumming and film removal of tarpaulin, cumbersome process, etc., to achieve Improve the effect of scale precipitation, beautiful and diversified style design, and simplify the process flow
- Summary
- Abstract
- Description
- Claims
- Application Information
AI Technical Summary
Problems solved by technology
Method used
Image
Examples
Embodiment 1
[0028] Such as figure 2 Shown, the concrete steps of production technology of the present invention are as follows:
[0029] (1) Put the woven cloth 2 on the cloth rack 1, manually adjust the level, send it into the first preheating tension roller 3 and the second preheating tension roller 4, and set the preheating temperature to 130°C;
[0030] (2) 30kg lignin and 10kg polyhydroxyalkanoate are mixed and put into the first screw extruder 5 and the second screw extruder 6 respectively, and the adhesive 7 is extruded on the first rubber roller 8 and the second rubber roller. Between the rollers 9 and between the fourth rubber roller 11 and the third rubber roller 10, the woven cloth 2 is sent into the second rubber roller and the third rubber roller for double-sided gluing; then the temperature of the temperature control device 13 is set to 170 ℃, drying and shaping the double-sided viscose cloth 14 at the first temperature control device 13;
[0031] (3) In the first laminat...
Embodiment 2
[0035] Such as figure 2 Shown, the concrete steps of production technology of the present invention are as follows:
[0036] (1) Put the woven cloth 2 on the cloth rack 1, manually adjust the level, send it into the first preheating tension roller 3 and the second preheating tension roller 4, and set the preheating temperature to 150°C;
[0037] (2) with step (2) in embodiment 1;
[0038](3) In the first laminating machine 15 and the second laminating machine 16, add the TPU laminating solution of the same composition respectively: thermoplastic polyurethane 60kg, aliphatic diisocyanate 5kg, isooctyl p-methoxycinnamate 10kg, Anatase nano-titanium dioxide 5kg, hydroxypropyl distarch phosphate 3kg, marshmallow gum 1.5kg, α-cyclodextrin 3kg, butyl regenerated rubber 2kg, paraffin oil 2kg, zinc myristate 0.5kg, purified water 8kg . The TPU laminating liquid is extruded between the first upper pressing roller 18 and the first lower pressing roller 19 and the second upper pressi...
Embodiment 3
[0042] Such as figure 2 Shown, the concrete steps of production technology of the present invention are as follows:
[0043] (1) Put the woven cloth 2 on the cloth rack 1, manually adjust the level, and send it into the first preheating tension roller 3 and the second preheating tension roller 4, and set the preheating temperature to 140°C;
[0044] (2) with step (2) in embodiment 1;
[0045] (3) In the first laminating machine 15 and the second laminating machine 16, add the TPU laminating solution of the same component respectively: thermoplastic polyurethane 55kg, aliphatic diisocyanate 8kg, isooctyl p-methoxycinnamate 12kg, Anatase nano-titanium dioxide 10kg, hydroxypropyl distarch phosphate 3kg, marshmallow gum 1kg, α-cyclodextrin 4kg, butyl regenerated rubber 2kg, paraffin oil 2kg, zinc myristate 0.5kg, purified water 2.5kg . The TPU laminating liquid is extruded between the first upper pressing roller 18 and the first lower pressing roller 19 and the second upper pr...
PUM
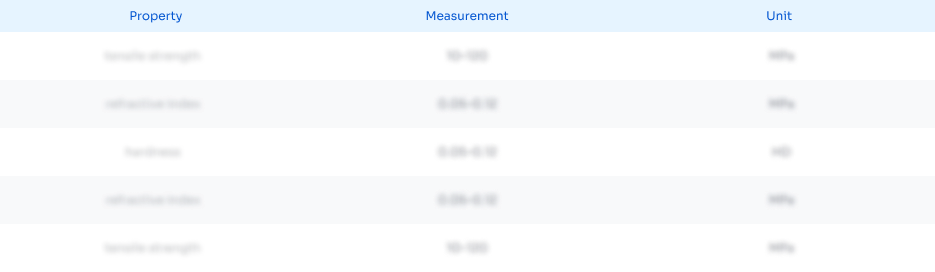
Abstract
Description
Claims
Application Information

- Generate Ideas
- Intellectual Property
- Life Sciences
- Materials
- Tech Scout
- Unparalleled Data Quality
- Higher Quality Content
- 60% Fewer Hallucinations
Browse by: Latest US Patents, China's latest patents, Technical Efficacy Thesaurus, Application Domain, Technology Topic, Popular Technical Reports.
© 2025 PatSnap. All rights reserved.Legal|Privacy policy|Modern Slavery Act Transparency Statement|Sitemap|About US| Contact US: help@patsnap.com