A kind of method of gold-tin alloy separation
A technology of tin alloy and alloy, applied in the field of gold-tin alloy separation, can solve problems such as long process
- Summary
- Abstract
- Description
- Claims
- Application Information
AI Technical Summary
Problems solved by technology
Method used
Image
Examples
Embodiment 1
[0024] Sulfur is added according to 1.2 times the mole fraction of the vulcanizing agent required for the non-sulfurized tin in the gold-tin alloy (mass percentage: Sn98.22%, Au1.49%, others <0.3%) to change to the vulcanized state.
[0025] Mix the gold-tin alloy and sulfur evenly, put it into an airtight container and seal it, and heat it up for vulcanization under the condition of anaerobic and stirring. Firstly, the temperature is controlled at 200°C to 250°C, and the reaction is carried out for 60 minutes. Then maintain anaerobic and stirring conditions, and raise the temperature to 380 ° C ~ 400 ° C, so that the material and vulcanizing agent undergo a deep vulcanization reaction. After the reaction is over, stop heating, and take out the sulfurized product after the material is cooled.
[0026] After vulcanization, the material was vacuum distilled for 90 minutes at a temperature of 1400° C. and a vacuum degree of 5 to 50 Pa to obtain volatiles and residues. The detec...
Embodiment 2
[0028] Sulfur is added according to 1.1 times the mole fraction of the vulcanizing agent required for the non-sulfurized tin in the gold-tin alloy (mass percentage: Sn89.66%, Au10.32%) to change into a sulfide state.
[0029] Mix the gold-tin alloy and sulfur evenly, put it into an airtight container and seal it, and heat it up for vulcanization under the condition of anaerobic and stirring. Firstly, the temperature is controlled at 230° C. to 280° C., and the reaction is carried out for 30 minutes. Then maintain anaerobic and stirring conditions, and raise the temperature to 350 ° C ~ 400 ° C, so that the material and vulcanizing agent undergo a deep vulcanization reaction. After the reaction is over, stop heating, and take out the sulfurized product after the material is cooled.
[0030] After vulcanization, the material was vacuum distilled for 60 minutes at a temperature of 1100° C. and a vacuum degree of 1 to 20 Pa to obtain volatiles and residues. The detected volatile...
Embodiment 3
[0032] Sulfur is added according to 1.15 times the mole fraction of the vulcanizing agent required for the non-sulfurized tin in the gold-tin alloy (mass percentage: Sn57.66%, Au42.32%) to change into a sulfide state.
[0033] Mix the gold-tin alloy and sulfur evenly, put it into an airtight container and seal it, and heat it up for vulcanization under the condition of anaerobic and stirring. Firstly, the temperature is controlled at 250° C. to 300° C., and the reaction is carried out for 30 minutes. Then maintain anaerobic and stirring conditions, and raise the temperature to 450 ° C ~ 500 ° C, so that the material and vulcanizing agent undergo a deep vulcanization reaction. After the reaction is over, stop heating, and take out the sulfurized product after the material is cooled.
[0034] After vulcanization, the material was vacuum distilled for 60 minutes at a temperature of 1300° C. and a vacuum degree of 30-100 Pa to obtain volatiles and residues. The detected volatile...
PUM
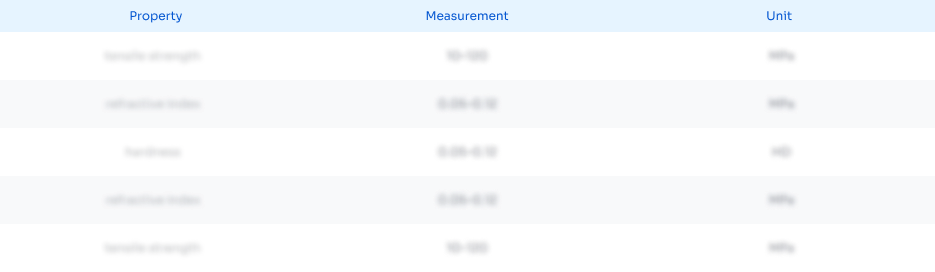
Abstract
Description
Claims
Application Information

- R&D
- Intellectual Property
- Life Sciences
- Materials
- Tech Scout
- Unparalleled Data Quality
- Higher Quality Content
- 60% Fewer Hallucinations
Browse by: Latest US Patents, China's latest patents, Technical Efficacy Thesaurus, Application Domain, Technology Topic, Popular Technical Reports.
© 2025 PatSnap. All rights reserved.Legal|Privacy policy|Modern Slavery Act Transparency Statement|Sitemap|About US| Contact US: help@patsnap.com