Thixotropic foam silicone rubber and preparation method thereof
A silicone rubber and foam technology, applied in the field of thixotropic foamed silicone rubber and its preparation, can solve the problems of complex process, limited application of foamed silicone rubber, and high preparation cost of thixotropic silicone rubber, and achieves wide application, low cost and smooth surface. Effect
- Summary
- Abstract
- Description
- Claims
- Application Information
AI Technical Summary
Problems solved by technology
Method used
Image
Examples
Embodiment 1
[0039] A thixotropic foam silicone rubber, which is prepared by mixing component A and component B according to an equal mass ratio; component A:
[0040]
[0041] B component:
[0042]
[0043] Weigh the required raw materials for A and B components according to the above formula:
[0044] Weigh α, ω-hydroxyl-terminated polydimethylsiloxane, heavy calcium carbonate, vinyl silicone oil and carbon black into a kneader according to the amount, dehydrate and knead for 180 minutes at a temperature of 120°C under vacuum, and cool to obtain Base A. Then add the base material A, hydrogen-containing silicone oil, and diallyl maleate into the planetary mixer, mix for 15 minutes, then add rod-shaped calcium carbonate according to the amount, stir and mix for 30 minutes, and vacuum stir for 20 minutes to obtain component A.
[0045]Weigh α, ω-hydroxyl-terminated polydimethylsiloxane, vinyl silicone oil and heavy calcium carbonate into a kneader, knead at a temperature of 120°C fo...
Embodiment 2
[0048] A thixotropic foam silicone rubber, which is prepared by mixing component A and component B according to an equal mass ratio; component A:
[0049]
[0050]
[0051] B component:
[0052]
[0053] Weigh the required raw materials for A and B components according to the above formula:
[0054] Weigh α, ω-hydroxyl-terminated polydimethylsiloxane, quartz sand, vinyl silicone oil and carbon black into a kneader according to the amount, dehydrate and knead for 240 minutes at a temperature of 130°C under vacuum, and cool to obtain the base material a. Then add the base material A, hydrogen-containing silicone oil, and diallyl maleate into the planetary mixer, mix for 15 minutes, then add rod-shaped calcium carbonate according to the amount, stir and mix for 30 minutes, and vacuum stir for 20 minutes to obtain component A.
[0055] Weigh α, ω-hydroxyl-terminated polydimethylsiloxane, vinyl silicone oil and heavy calcium carbonate into a kneader, knead at a temperatu...
Embodiment 3
[0058] A thixotropic foam silicone rubber, which is prepared by mixing component A and component B according to an equal mass ratio; component A:
[0059]
[0060] B component:
[0061]
[0062] Weigh the required raw materials for A and B components according to the above formula:
[0063] Weigh α, ω-terminated hydroxyl polydimethylsiloxane, heavy calcium carbonate, vinyl silicone oil and phthalocyanine blue into a kneader, dehydrate and knead for 180 minutes at a temperature of 120°C in a vacuum state, and cool down. Get base material A. Then add the base material A, hydrogen-containing silicone oil, and phenylacetylene into the planetary mixer, mix for 15 minutes, then add rod-shaped calcium carbonate according to the amount, stir and mix for 30 minutes, and vacuum stir for 20 minutes to obtain component A.
[0064] Weigh α, ω-hydroxyl-terminated polydimethylsiloxane, vinyl silicone oil and heavy calcium carbonate into a kneader, knead at a temperature of 120°C for ...
PUM
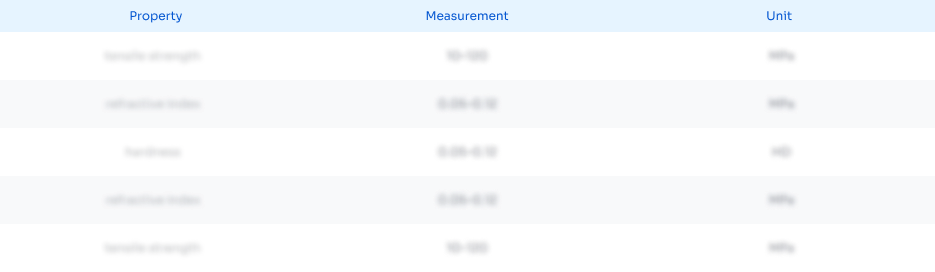
Abstract
Description
Claims
Application Information

- R&D Engineer
- R&D Manager
- IP Professional
- Industry Leading Data Capabilities
- Powerful AI technology
- Patent DNA Extraction
Browse by: Latest US Patents, China's latest patents, Technical Efficacy Thesaurus, Application Domain, Technology Topic, Popular Technical Reports.
© 2024 PatSnap. All rights reserved.Legal|Privacy policy|Modern Slavery Act Transparency Statement|Sitemap|About US| Contact US: help@patsnap.com