A method for preparing superhydrophobic microporous membranes by synergistically regulating phase separation with aqueous inorganic salt solution
An inorganic salt solution and phase separation technology, applied in the field of membrane separation, can solve problems such as easy shedding, unsuitable for mass production, and reduced flux, and achieve an effect that is conducive to aggregation
- Summary
- Abstract
- Description
- Claims
- Application Information
AI Technical Summary
Problems solved by technology
Method used
Image
Examples
Embodiment 1
[0064] Mix 110.6g of dimethylacetamide, 30g of polyvinylidene fluoride, 39g of propylene glycol and water, and 5ml of sodium chloride aqueous solution (the mass percentage of sodium chloride aqueous solution is 3.7%), and the temperature of the casting solution is 90°C. The scraping film was cast on the board, and the solvent volatilization time was 60s.
[0065] The resulting membrane has a contact angle of 155° and a water flux of 52 L / m 2 .h.
Embodiment 2
[0070] Mix 110.6g of dimethylacetamide, 30g of polyvinylidene fluoride, 39g of amyl alcohol and water, and 5ml of potassium nitrate aqueous solution (the mass percentage of potassium nitrate aqueous solution is 3.7%) and mix uniformly. The temperature of the casting solution is 90°C. The scraping film was cast on the top, and the solvent volatilization time was 60s.
[0071] The resulting membrane has a contact angle of 143° and a water flux of 38 L / m 2 .h.
Embodiment 3
[0073] Mix 110.6g of dimethylformamide, 30g of polyvinylidene fluoride, 39g of water and butanol, and 5ml of sodium nitrate aqueous solution (the mass percentage of sodium nitrate aqueous solution is 3.7%). The scraping film was cast on the board, and the solvent evaporation time was 60s.
[0074] The resulting membrane has a contact angle of 144° and a water flux of 44L / m 2 .h.
PUM
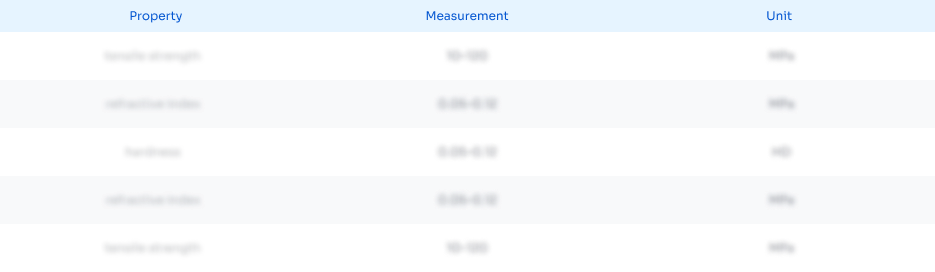
Abstract
Description
Claims
Application Information

- R&D
- Intellectual Property
- Life Sciences
- Materials
- Tech Scout
- Unparalleled Data Quality
- Higher Quality Content
- 60% Fewer Hallucinations
Browse by: Latest US Patents, China's latest patents, Technical Efficacy Thesaurus, Application Domain, Technology Topic, Popular Technical Reports.
© 2025 PatSnap. All rights reserved.Legal|Privacy policy|Modern Slavery Act Transparency Statement|Sitemap|About US| Contact US: help@patsnap.com