Thermal-insulation and heat-preservation material with cold resistance and preparation method thereof
A heat-insulation and cold-resistance technology, applied in the field of cold-resistance heat-insulation and heat-insulation materials and their preparation, can solve the problems of reduced heat-insulation performance, high thermal conductivity, easy to burn, etc., to improve toughness and cold-resistance, reduce thermal conductivity, Improve the effect of poor cold resistance
- Summary
- Abstract
- Description
- Claims
- Application Information
AI Technical Summary
Problems solved by technology
Method used
Image
Examples
Embodiment 1
[0021] (1) 8 parts of hollow glass microspheres, 50 parts of polyphenylene particles, 8 parts of clay, and 10 parts of quartz sand are pulverized and then stirred and mixed evenly;
[0022] (2) Add 10 parts of allyl methacrylate, 8 parts of cyclopentanol, 20 parts of 4-aminobutyric acid, and 5 parts of di-n-hexyl azelate to step (1), and react for 8 hours at a water bath temperature of 80°C ;
[0023] (3) Add 5 parts of alkyl diphenyl phosphate, 6 parts of ethyl nonanoate, 7 parts of N,N-dimethylurea, and 4 parts of polyacrylamide, and stir at a temperature of 80°C to form a foamy mixture;
[0024] (4) Concentrate the foamy mixture by suction filtration, and control the mass percent content of the solid phase in the foam slurry to 8%;
[0025] (5) Compress it into a prefabricated body, control the compression amount to 60%, and the density to 0.2g / cm 3 ;Dried at 160°C, melt extruded and granulated.
Embodiment 2
[0027] (1) After pulverizing 12 parts of hollow glass microspheres, 40 parts of polyphenylene particles, 10 parts of clay and 5 parts of quartz sand, stir and mix them evenly;
[0028] (2) Add 15 parts of allyl methacrylate, 12 parts of cyclopentanol, 10 parts of 4-aminobutyric acid, and 10 parts of di-n-hexyl azelate to step (1), and react for 12 hours at a water bath temperature of 60°C ;
[0029] (3) Add 8 parts of alkyl diphenyl phosphate, 9 parts of ethyl nonanoate, 10 parts of N,N-dimethylurea, and 6 parts of polyacrylamide, and stir at a temperature of 100°C to form a foamy mixture;
[0030] (4) Concentrate the foamy mixture by suction filtration, and control the mass percent content of the solid phase in the foam slurry to 20%;
[0031] (5) Compress it into a prefabricated body, control the compression amount to 20%, and the density to 0.4g / cm 3 ;Dried at 200°C, melt extruded and granulated.
Embodiment 3
[0033] (1) After pulverizing 10 parts of hollow glass microspheres, 40 parts of polyphenylene particles, 8 parts of clay and 7 parts of quartz sand, stir and mix them evenly;
[0034] (2) Add 12 parts of allyl methacrylate, 9 parts of cyclopentanol, 12 parts of 4-aminobutyric acid, and 7 parts of di-n-hexyl azelate to step (1), and react for 10 hours at a water bath temperature of 65°C ;
[0035] (3) Add 7 parts of alkyl diphenyl phosphate, 8 parts of ethyl nonanoate, 9 parts of N,N-dimethylurea, and 5 parts of polyacrylamide, and stir at a temperature of 85°C to form a foamy mixture;
[0036] (4) Concentrate the foamy mixture by suction filtration, and control the mass percent content of the solid phase in the foam slurry to 15%;
[0037] (5) Compress it into a preform, control the compression amount to 35%, and the density to 0.25g / cm 3 ;Dried at 180°C, melt extruded and granulated.
PUM
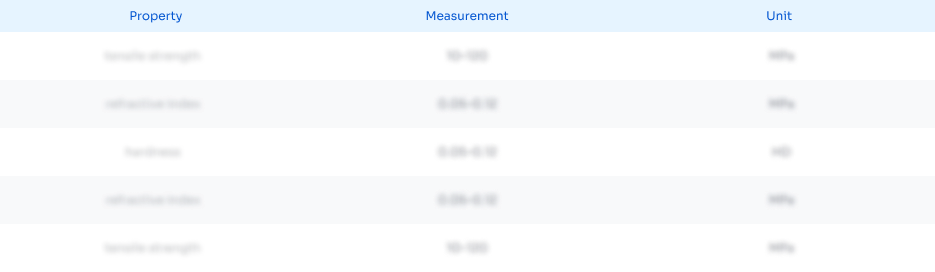
Abstract
Description
Claims
Application Information

- Generate Ideas
- Intellectual Property
- Life Sciences
- Materials
- Tech Scout
- Unparalleled Data Quality
- Higher Quality Content
- 60% Fewer Hallucinations
Browse by: Latest US Patents, China's latest patents, Technical Efficacy Thesaurus, Application Domain, Technology Topic, Popular Technical Reports.
© 2025 PatSnap. All rights reserved.Legal|Privacy policy|Modern Slavery Act Transparency Statement|Sitemap|About US| Contact US: help@patsnap.com