Method for modifying layered silicate powder by using silicon dioxide
A technology of silicate powder and layered silicate, applied in chemical instruments and methods, fibrous fillers, inorganic pigment treatment, etc., can solve problems such as high price and achieve the effect of reducing production costs
- Summary
- Abstract
- Description
- Claims
- Application Information
AI Technical Summary
Problems solved by technology
Method used
Image
Examples
Embodiment 1
[0047] Dilute water glass with modulus 3.24 of 3401 from Qingdao Dongyue Soda Soda Factory with deionized water to a solid content of 3%, and pass it through a cation exchange resin to obtain an orthosilicic acid solution. Add 1M sulfuric acid to the solution to adjust its pH to 1. After aging for 72 hours at room temperature, let it pass through the anion exchange resin first, and then immediately pass through the cation exchange resin to obtain an acidic activated orthosilicic acid solution.
[0048] Add 3% water glass to the acidic activated ortho silicic acid solution to adjust its pH to 10 to obtain an alkaline activated ortho silicic acid solution. Take 250ml of alkaline activated orthosilicic acid solution as the base solution, use the constant liquid level method to control the liquid temperature to 85°C, and add active silicic acid dropwise to it at a rate of 0.6ml / min, and add 200ml dropwise after 5 hours After acidic activation of the orthosilicic acid solution, lig...
Embodiment 2
[0052] Dilute water glass with modulus 3.24 of 3401 from Qingdao Dongyue Soda Soda Factory with deionized water to a solid content of 5%, and pass it through a cation exchange resin to obtain an orthosilicic acid solution. Add 1M hydrochloric acid to the solution to adjust its pH to 2. After aging at room temperature for 48 hours, let it pass through the anion exchange resin first, and then immediately pass through the cation exchange resin to obtain an acidic activated orthosilicic acid solution.
[0053] Add 1M sodium hydroxide solution to the acidic activated orthosilicic acid solution to adjust its pH to 8. Take 250ml of alkaline activated orthosilicic acid solution as the base solution, use the constant liquid level method to control the liquid temperature to 65°C, and add acidic activated orthosilicic acid solution dropwise at a rate of 0.4ml / min, after 8 hours And after adding 200ml of acidic activated orthosilicic acid solution dropwise, light blue opalescence appeared...
Embodiment 3
[0057] Dilute water glass with modulus 3.24 of 3401 from Qingdao Dongyue Soda Soda Factory with deionized water to a solid content of 4%, and pass it through a cation exchange resin to obtain an orthosilicic acid solution. Add 1M nitric acid to the solution to adjust its pH to 2. After aging at room temperature for 48 hours, let it pass through the anion exchange resin first, and then immediately pass through the cation exchange resin to obtain an acidic activated orthosilicic acid solution.
[0058] Add 1M ammonia solution to the acidic activated orthosilicic acid solution to adjust its pH to 10. Take 250ml of alkaline activated orthosilicic acid solution as the base solution, use the constant liquid level method to control the liquid temperature to 70°C, and add acidic activated orthosilicic acid solution to it at a rate of 0.4ml / min, after 6 hours And after adding 150ml of acidic activated orthosilicic acid solution dropwise, light blue opalescence appeared in the bottom li...
PUM
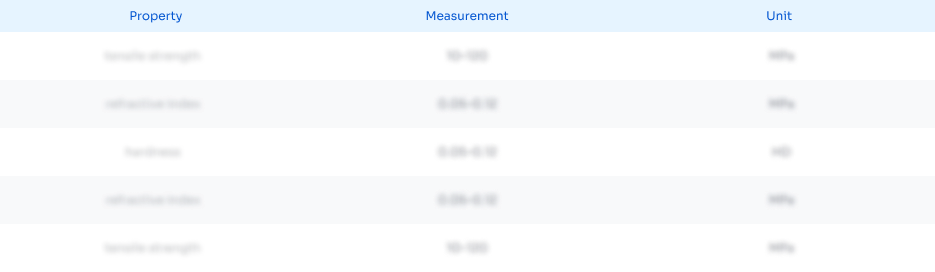
Abstract
Description
Claims
Application Information

- R&D
- Intellectual Property
- Life Sciences
- Materials
- Tech Scout
- Unparalleled Data Quality
- Higher Quality Content
- 60% Fewer Hallucinations
Browse by: Latest US Patents, China's latest patents, Technical Efficacy Thesaurus, Application Domain, Technology Topic, Popular Technical Reports.
© 2025 PatSnap. All rights reserved.Legal|Privacy policy|Modern Slavery Act Transparency Statement|Sitemap|About US| Contact US: help@patsnap.com