Method for preparing sintered brick by water-based well drilling condensate modification
A technology for curing and sintering bricks, used in clay products, applications, household appliances, etc., can solve the problems of brick body bursting, powdering, frosting, brick body whitening, etc., to solve the problem of whitening, simple process and optimization. The effect of the process method
- Summary
- Abstract
- Description
- Claims
- Application Information
AI Technical Summary
Problems solved by technology
Method used
Image
Examples
Embodiment 1
[0029] A method for preparing sintered bricks by modifying water-based drilling solidifieds, comprising the following steps:
[0030] (1) After preliminary crushing of the water-based drilling solidified material, it is transported to a rotary circular screen to remove most of the limestone until its content is less than 10%, and then the water-based drilling solidified material with limestone removed is transported to the impact hammer crusher Perform deep crushing treatment in the middle, and then sieve with a vibrating sieve with a mesh diameter of 10-20 mesh to obtain a powder with a fineness of less than 1mm;
[0031] (2) The water-based drilling solidification powder obtained in step (1) and modifier barium salt, shale soil, and internal combustion coal are by weight percentage: water-based drilling solidification powder 15%, modifier barium salt 2% , 70% of shale soil, 13% of internal combustion coal, mixed and stirred evenly to obtain a mixed material;
[0032] (3) Ad...
Embodiment 2
[0036] A method for preparing sintered bricks by modifying water-based drilling solidifieds, comprising the following steps:
[0037] (1) After preliminary crushing, the water-based drilling solidified material is sent to the stone remover to remove most of the limestone until its content is less than 10%, and then the water-based drilling solidified material with limestone removed is transported to the impact hammer crusher Carry out deep crushing treatment, and then sieve with a vibrating sieve with a screen aperture of 10-20 mesh to obtain a powder with a fineness of less than 1mm;
[0038] (2) The water-based drilling solidification powder obtained in step (1) and modifier barium salt, shale soil, and internal combustion coal are in percentage by weight: water-based drilling solidification powder 30%, barium nitrate 7.5%, shale Soil 50%, internal combustion coal 12.5%, mix and stir evenly to obtain the mixed material;
[0039] (3) Add water to the mixed material obtained ...
Embodiment 3
[0042] A method for preparing sintered bricks by modifying water-based drilling solidifieds, comprising the following steps:
[0043] (1) Pretreatment of water-based drilling solidified material: first, crush the water-based drilling solidified material, transport it to the stone remover with a belt conveyor, remove most of the limestone, and then continue to use the belt conveyor to remove the limestone-removed water The base drilling solidified material is transported to the impact hammer crusher for deep crushing treatment. After the crushing treatment, it is screened with a vibrating screen. The mesh diameter of the vibrating screen is 10-20 mesh, and the powder with a fineness of less than 1mm is obtained;
[0044] (2) Ingredients: Add the following raw material components and modifiers by weight percentage: 25% of water-based drilling solidification powder, 5% of barium chloride, 55% of shale soil, 15% of internal combustion coal, fully stir and mix evenly , to get the m...
PUM
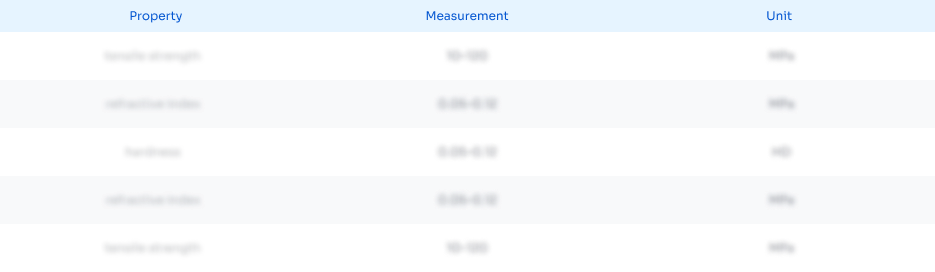
Abstract
Description
Claims
Application Information

- R&D
- Intellectual Property
- Life Sciences
- Materials
- Tech Scout
- Unparalleled Data Quality
- Higher Quality Content
- 60% Fewer Hallucinations
Browse by: Latest US Patents, China's latest patents, Technical Efficacy Thesaurus, Application Domain, Technology Topic, Popular Technical Reports.
© 2025 PatSnap. All rights reserved.Legal|Privacy policy|Modern Slavery Act Transparency Statement|Sitemap|About US| Contact US: help@patsnap.com