Method for preparing zinc sulfate monohydrate from zinc-containing waste residue
A technology for zinc sulfate and waste sulfuric acid, which is applied in the preparation of zinc sulfate and zinc compounds, chemical instruments and methods, etc., can solve problems such as difficulty in recycling, and achieve the effects of low cost, easy promotion, and high purity
- Summary
- Abstract
- Description
- Claims
- Application Information
AI Technical Summary
Problems solved by technology
Method used
Image
Examples
Embodiment 1
[0028] The production raw material contains zinc waste residue, calculated by weight percentage, containing 40-60% of zinc, 2-4% of iron, 3-5% of copper, 10-20% of cadmium and 8-16% of silicon oxide.
[0029] The present embodiment prepares the method for zinc sulfate monohydrate from zinc-containing waste residue, and its preparation method is as follows:
[0030] (1) Acid leaching: add zinc-containing waste residue and sulfuric acid with a weight percentage of 20-30% to the first acid leaching tank in a weight ratio of 1:3, and continue to stir for 2 hours. At the end of the reaction, control the pH to 4.8-5.0, press filter Perform liquid-solid separation to obtain primary filtrate and primary filter residue;
[0031] (2) Oxidative iron removal: put the primary filtrate in the iron removal tank, heat it to 70°C, introduce air or oxygen and stir, the color of the filtrate changes from colorless to rust red, and detect the concentration of ferric ion. 3+ When the content is l...
Embodiment 2
[0038] The production raw material contains zinc waste residue, calculated by weight percentage, containing 40-60% of zinc, 2-4% of iron, 3-5% of copper, 10-20% of cadmium and 8-16% of silicon oxide.
[0039] The method for preparing zinc sulfate monohydrate from zinc-containing waste residue, its preparation method is as follows:
[0040](1) Acid leaching: Add zinc-containing waste slag and factory waste sulfuric acid with a weight percentage of 20 to 30% to the first acid leaching tank in a weight ratio of 1:3, and continue stirring for 2 hours. At the end of the reaction, the pH is controlled to be 4.8 to 5.0, Press filtration for liquid-solid separation to obtain the primary filtrate and primary filter residue; then in the second acid leaching step, the primary filter residue and 20-30% of factory waste sulfuric acid are added to the second acid leaching tank in a weight ratio of 1:4, and heated to The temperature is 30-40°C, continuous stirring for 2.5-3 hours, the pH is ...
Embodiment 3
[0052] The production raw material contains zinc waste residue, calculated by weight percentage, containing 40-60% of zinc, 2-4% of iron, 3-5% of copper, 10-20% of cadmium and 8-16% of silicon oxide.
[0053] The present embodiment prepares the method for zinc sulfate monohydrate from zinc-containing waste residue, and its preparation method is as follows:
[0054] (1) Acid leaching: add zinc-containing waste residue and sulfuric acid with a weight percentage of 20-30% to the first acid leaching tank in a weight ratio of 1:3, and continue to stir for 2 hours. At the end of the reaction, control the pH to 4.8-5.0, press filter Perform liquid-solid separation to obtain primary filtrate and primary filter residue;
[0055] (2) Oxidative iron removal: put the primary filtrate in the iron removal tank, heat to 75°C, feed air or oxygen and stir at a stirring speed of 800r / min, and the gas flow rate of the air or oxygen is 6-8L / min , the color of the filtrate changed from colorless ...
PUM
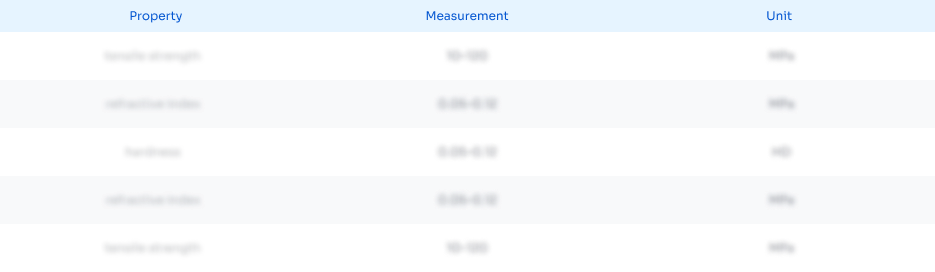
Abstract
Description
Claims
Application Information

- R&D
- Intellectual Property
- Life Sciences
- Materials
- Tech Scout
- Unparalleled Data Quality
- Higher Quality Content
- 60% Fewer Hallucinations
Browse by: Latest US Patents, China's latest patents, Technical Efficacy Thesaurus, Application Domain, Technology Topic, Popular Technical Reports.
© 2025 PatSnap. All rights reserved.Legal|Privacy policy|Modern Slavery Act Transparency Statement|Sitemap|About US| Contact US: help@patsnap.com