Method for machining automobile spare parts
A technology of auto parts and bushings, applied in the field of mechanical processing, can solve the problems of increasing company expenses, unfavorable company development, and accelerating motor damage speed, etc., to achieve convenient loading and unloading, reduce damage probability, and clamping effect good effect
- Summary
- Abstract
- Description
- Claims
- Application Information
AI Technical Summary
Problems solved by technology
Method used
Image
Examples
Embodiment Construction
[0020] The present invention will be described in further detail below by means of specific embodiments:
[0021] The reference signs in the drawings of the specification include: base 1, clamping tube 2, rotating tube 3, casing 4, pressing rod 5, clamping rod 6, first bearing seat 7, second bearing seat 8, toggle Rod 9, motor 10, pulley 11, reducer 12, convex strip 13, groove 14, conical truncated 15, toggle groove 16, support bar 17, clamp 18, rubber layer 19, clip bar 20, support bar 21 , stroke hole 22, tubular auto parts 23, limit rod 24.
[0022] The method used for auto parts processing, such as figure 1 , figure 2 The auto parts processing device shown includes a base 1, a clamping tube 2, a rotating tube 3, a casing 4, two pressing rods 5, two clamping rods 6, a first bearing seat 7, and a second bearing seat 8 , toggle lever 9 and motor 10. The first bearing seat 7 and the second bearing seat 8 are fixed on the base 1 , and the first bearing seat 7 is located on...
PUM
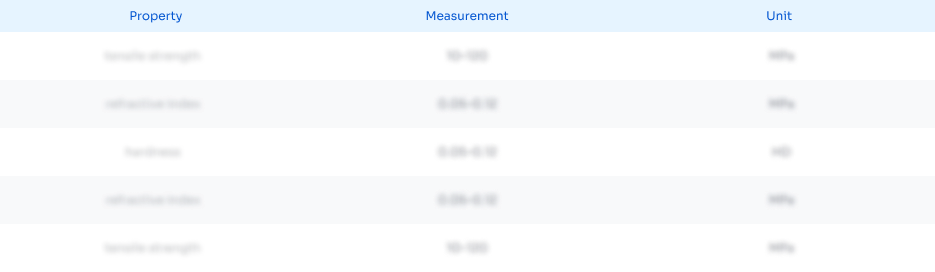
Abstract
Description
Claims
Application Information

- Generate Ideas
- Intellectual Property
- Life Sciences
- Materials
- Tech Scout
- Unparalleled Data Quality
- Higher Quality Content
- 60% Fewer Hallucinations
Browse by: Latest US Patents, China's latest patents, Technical Efficacy Thesaurus, Application Domain, Technology Topic, Popular Technical Reports.
© 2025 PatSnap. All rights reserved.Legal|Privacy policy|Modern Slavery Act Transparency Statement|Sitemap|About US| Contact US: help@patsnap.com