Heat treatment process for high-performance disc cutter of TBM
A disc-shaped hob, high-performance technology, applied in the field of heat treatment, can solve the problems of unreasonable carbide morphology, size and distribution, reducing the service life of disc-shaped hob, coarse grain size, etc., to shorten the construction period, Improve the service life and the effect of uniform and fine grain size
- Summary
- Abstract
- Description
- Claims
- Application Information
AI Technical Summary
Problems solved by technology
Method used
Image
Examples
Embodiment 1
[0035] In this embodiment, the composition and mass percentage of the disc hob for TBM are: carbon 0.50%; silicon 1.00%; manganese 0.40%; chromium 5.20%; nickel 0.25%; molybdenum 1.35%; vanadium 1.27%; Sulfur 0.006%; the balance is iron.
[0036] In this embodiment, the heat treatment process includes the following steps: 1) Heating the disc-shaped hob to 860°C at 150°C / h, keeping it warm for 2.5 hours, slowly cooling to 590°C at 20°C / h, and cooling to room temperature with the furnace ; 2) First, heat the disc-shaped hob to 1050 °C at 150 °C / h, keep it warm for 2.5 hours, and quickly cool it to 310 °C at 120 °C / h; secondly, heat the disc-shaped hob at 150 °C / h to 1050°C, keep warm for 2.5 hours, quickly cool at 120°C / h to 310°C; then, heat the disc hob at 150°C / h to 860°C, keep warm for 2.5 hours, cool down at 80°C to 735°C, hold for 4.5 h, cool to room temperature with the furnace; 3) Quenching process: heat the disc-shaped hob to 1050 °C at 150 °C / h, keep warm for 2.5 hour...
Embodiment 2
[0039] In this embodiment, the composition and mass percentage of the disc hob for TBM are: carbon 0.48%; silicon 1.15%; manganese 0.26%; chromium 5.70%; nickel 0.18%; molybdenum 1.43%; vanadium 0.88%; Sulfur 0.005%; the balance is iron.
[0040]In this embodiment, the heat treatment process includes the following steps: 1) heating the disc-shaped hob to 850°C at 120°C / h, keeping it warm for 2 hours, slowly cooling at 10°C / h to a temperature of 580°C, and cooling to room temperature with the furnace; 2) First, heat the disc-shaped hob to 1040 °C at 120 °C / h, keep it warm for 2 hours, and quickly cool it to 300 °C at 100 °C / h; secondly, heat the disc-shaped hob to 1040 °C at 120 °C / h , keep warm for 2 hours, and quickly cool at 100°C / h to 300°C; then, heat the disc hob at 120°C / h to 850°C, hold for 2 hours, cool down at 60°C to 730°C, hold for 4 hours, and cool with the furnace to room temperature; 3) Quenching process: heat the disc-shaped hob to 1040 °C at 120 °C / h, keep war...
Embodiment 3
[0043] In this embodiment, the composition and mass percentage of the disc hob for TBM are: carbon 0.55%; silicon 0.82%; manganese 0.57%; chromium 4.51%; nickel 0.38%; molybdenum 1.19%; vanadium 1.36%; Sulfur 0.007%; the balance is iron.
[0044] In this embodiment, the heat treatment process includes the following steps: 1) heating the disc-shaped hob to 870°C at 180°C / h, keeping it warm for 3 hours, slowly cooling to 600°C at 30°C / h, and cooling to room temperature with the furnace; 2) First, heat the disc-shaped hob to 1060 °C at 180 °C / h, keep it warm for 3 hours, and quickly cool it to 320 °C at 130 °C / h; secondly, heat the disc-shaped hob to 1060 °C at 180 °C / h , keep it warm for 3 hours, and quickly cool it at 130°C / h to 320°C; then, heat the disc hob at 180°C / h to 870°C, keep it at 3h, cool it at 100°C to 740°C, keep it at 5h, and cool it with the furnace to room temperature; 3) Quenching process: heat the disc-shaped hob to 1060 °C at 180 °C / h, keep warm for 3 hours,...
PUM
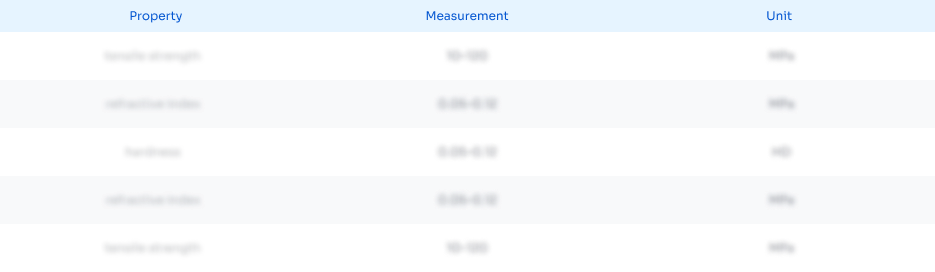
Abstract
Description
Claims
Application Information

- R&D
- Intellectual Property
- Life Sciences
- Materials
- Tech Scout
- Unparalleled Data Quality
- Higher Quality Content
- 60% Fewer Hallucinations
Browse by: Latest US Patents, China's latest patents, Technical Efficacy Thesaurus, Application Domain, Technology Topic, Popular Technical Reports.
© 2025 PatSnap. All rights reserved.Legal|Privacy policy|Modern Slavery Act Transparency Statement|Sitemap|About US| Contact US: help@patsnap.com