Composite base material polishing grinding apparatus and preparing method thereof
A composite substrate, polishing and grinding technology, used in chemical instruments and methods, abrasives, manufacturing tools, etc., can solve the problems of surface scratch quality, insufficient adhesion, and large stretchability of products, and achieve high mechanical strength and Heat and abrasion resistance, superior elasticity and softness, the effect of enhancing adhesion
- Summary
- Abstract
- Description
- Claims
- Application Information
AI Technical Summary
Problems solved by technology
Method used
Image
Examples
Embodiment 1
[0059] A composite substrate polishing abrasive, such as figure 1 As shown, it includes a composite base material and an abrasive 7 adhered to the composite base material. The composite base material is composed of a TPU film 3 and a PET film 1 through a modified adhesive 2 . The surface of the TPU film 3 of the composite substrate is coated with a primer layer 4 , an adhesive layer 4 and an anti-blocking coating 6 in sequence.
[0060] The preparation method of this composite substrate polishing abrasive tool is as follows:
[0061] Step a, preparation of modified adhesive 2:
[0062] a1, prepare modified polyurethane resin:
[0063] According to the weight ratio of polyurethane resin: epoxy resin: accelerator = 100:30:2, the polyurethane resin is first added to the reaction kettle, and the epoxy resin is added in the stirring state, then the temperature is raised to 60°C, and the reaction is carried out for 2 hours. Then lower the temperature to 20~30°C, then add the acce...
Embodiment 2
[0082] A composite substrate polishing abrasive, such as figure 1 As shown, it includes a composite base material and an abrasive 7 adhered to the composite base material. The composite base material is composed of a TPU film 3 and a PET film 1 through a modified adhesive 2 . The surface of the TPU film 3 of the composite substrate is coated with a primer layer 4 , an adhesive layer 4 and an anti-blocking coating 6 in sequence.
[0083] The preparation method of this composite substrate polishing abrasive tool is as follows:
[0084] Step a, preparation of modified adhesive 2:
[0085] a1, prepare modified polyurethane resin:
[0086] According to the weight ratio of polyurethane resin: epoxy resin: accelerator = 100:25:3, the polyurethane resin is first added to the reaction kettle, and the epoxy resin is added under stirring, then the temperature is raised to 55°C, and the reaction is 1.5 hours. Then lower the temperature to 20~30°C, then add the accelerator, and stir eve...
Embodiment 3
[0105] A composite substrate polishing abrasive, such as figure 1 As shown, it includes a composite base material and an abrasive 7 adhered to the composite base material. The composite base material is composed of a TPU film 3 and a PET film 1 through a modified adhesive 2 . The surface of the TPU film 3 of the composite substrate is coated with a primer layer 4 , an adhesive layer 4 and an anti-blocking coating 6 in sequence.
[0106] The preparation method of the composite substrate polishing abrasive is as follows: step a, preparation of modified adhesive 2:
[0107] a1, prepare modified polyurethane resin:
[0108] According to the weight ratio of polyurethane resin: epoxy resin: accelerator = 100:40:5, the polyurethane resin is first added to the reaction kettle, and the epoxy resin is added under stirring, then the temperature is raised to 65°C, and the reaction is 2.5 hours. Then lower the temperature to 20~30°C, then add the accelerator, and stir evenly to obtain th...
PUM
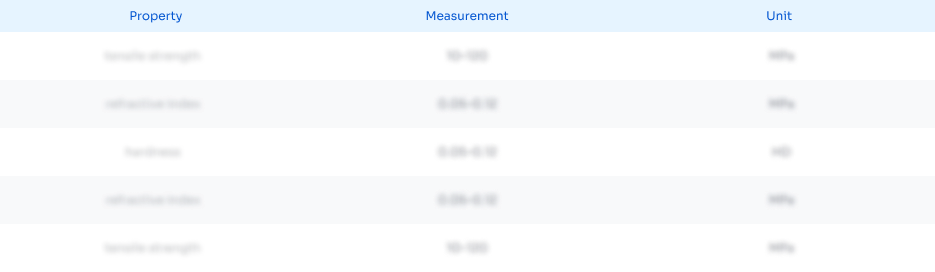
Abstract
Description
Claims
Application Information

- Generate Ideas
- Intellectual Property
- Life Sciences
- Materials
- Tech Scout
- Unparalleled Data Quality
- Higher Quality Content
- 60% Fewer Hallucinations
Browse by: Latest US Patents, China's latest patents, Technical Efficacy Thesaurus, Application Domain, Technology Topic, Popular Technical Reports.
© 2025 PatSnap. All rights reserved.Legal|Privacy policy|Modern Slavery Act Transparency Statement|Sitemap|About US| Contact US: help@patsnap.com