Sizing composition as well as preparation method and application thereof
A technology of composition and slurry, which is applied in the textile field, can solve the problems of low rubbing fastness, hard fabric feel, poor rubbing fastness, etc., and achieve high rubbing fastness, soft fabric feel and excellent adhesion Effect
- Summary
- Abstract
- Description
- Claims
- Application Information
AI Technical Summary
Problems solved by technology
Method used
Image
Examples
Embodiment 1
[0045] (1) Weigh 8.884g glyceride oil and 1.116g dichloromethane and put them in a container, dissolve them at 80°C, then add 0.2g disperse cationic pink, 0.6g crystal violet lactone and 3.0g bisphenol A and mix Seal well, and stir in a water bath at 80°C for 60 minutes to make a core material solution;
[0046] (2) Take 2.00g of melamine, 3.86g of formaldehyde solution and 22.5ml of distilled water, mix and stir evenly at a temperature of 70°C, adjust the pH value of the mixture to 8.5-9 with triethanolamine, and then react for 30 minutes until it is colorless and transparent shape, that is, to make a prepolymer, take it out and store it at 50°C for later use;
[0047] (3) Take 1.38g styrene-maleic anhydride copolymer and 25ml distilled water in a three-necked flask, and add 0.2gNaOH, mix thoroughly, then adjust the pH value of the solution to 4-5 with 10% citric acid, and place the solution at 50 Stirring and reacting at a temperature of ℃ for 1 h; then adding 0.966 g of em...
Embodiment 2
[0053] (1) Weigh 7.284g glyceride oil and 2.716g dichloromethane and put them in a container, dissolve them at 80°C, then add 0.2g disperse cationic rose, 0.6g crystal violet lactone and 3.0g bisphenol A and mix Seal well, and stir in a water bath at 80°C for 60 minutes to make a core material solution;
[0054] (2) Take 2.00g of melamine, 3.86g of formaldehyde solution and 22.5ml of distilled water, mix and stir evenly at a temperature of 70°C, adjust the pH value of the mixture to 8.5-9 with triethanolamine, and then react for 30 minutes until it is colorless and transparent shape, that is, to make a prepolymer, take it out and store it at 50°C for later use;
[0055] (3) Take 1.38g styrene-maleic anhydride copolymer and 25ml distilled water in a three-necked flask, and add 0.2gNaOH, mix thoroughly, then adjust the pH value of the solution to 4-5 with 10% citric acid, and place the solution at 50 Stirring and reacting at a temperature of ℃ for 1 h; then adding 0.966 g of em...
Embodiment 3
[0061] (1) Weigh 8.012g glyceride oil and 1.888g dichloromethane and put them in a container, dissolve them at 78°C, then add 0.1g disperse cationic pink, 0.7g crystal violet lactone and 3.0g bisphenol A and mix Seal well, and stir in a water bath at 80°C for 60 minutes to make a core material solution;
[0062] (2) Take 1.50g of melamine, 3.62g of formaldehyde solution and 22.5ml of distilled water, mix and stir evenly at a temperature of 70°C, adjust the pH value of the mixture to 8.5-9 with triethanolamine, and then react for 30 minutes until it is colorless and transparent shape, that is, to make a prepolymer, take it out and store it at 50°C for later use;
[0063] (3) Take 1.38g styrene-maleic anhydride copolymer and 25ml distilled water in a three-necked flask, and add 0.2gNaOH, mix thoroughly, then adjust the pH value of the solution to 4-5 with 10% citric acid, and place the solution at 50 Stirring and reacting at a temperature of ℃ for 1 h; then adding 0.966 g of em...
PUM
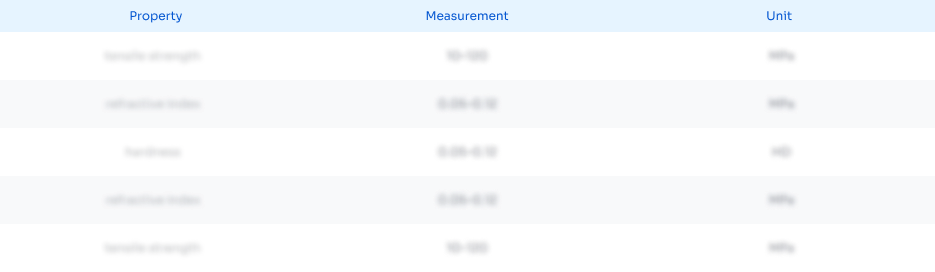
Abstract
Description
Claims
Application Information

- Generate Ideas
- Intellectual Property
- Life Sciences
- Materials
- Tech Scout
- Unparalleled Data Quality
- Higher Quality Content
- 60% Fewer Hallucinations
Browse by: Latest US Patents, China's latest patents, Technical Efficacy Thesaurus, Application Domain, Technology Topic, Popular Technical Reports.
© 2025 PatSnap. All rights reserved.Legal|Privacy policy|Modern Slavery Act Transparency Statement|Sitemap|About US| Contact US: help@patsnap.com