Resin button formula and production technology thereof
A button and resin technology, which is applied in the field of resin button formula and its production process, can solve the problems of high cost, high cost and easy breakage of m-benzene resin, so as to improve the anti-corrosion and wear-resistant effect, not easy to break, and prevent mutual penetration effect
- Summary
- Abstract
- Description
- Claims
- Application Information
AI Technical Summary
Problems solved by technology
Method used
Examples
Embodiment 1
[0018] The resin button components include 30 parts by weight of unsaturated polyester resin, 10 parts of calcium propionate, 5 parts of chitosan, 2 parts of glass fiber, 2 parts of microcrystalline wax, 2 parts of hollow glass microspheres, and 1 part of curing agent. 1 part, 1 part of cobalt naphthalate, 5 parts of color paste, 1 part of pearl powder and 2 parts of thixotropic agent.
[0019] The production technique of the present embodiment comprises the following steps:
[0020] A. Mix unsaturated polyester resin, calcium propionate, chitosan, glass fiber, microcrystalline wax, hollow glass microspheres, curing agent, cobalt naphthalate, color paste, pearl powder and thixotropic agent and add to the stirring tank Stir in medium, the stirring rate is 1000 rpm, and the stirring time is 10min, to obtain the mixture;
[0021] B, the mixing agent that step A obtains is added in the centrifuge barrel, adopts the bar casting method to make bar;
[0022] C, then carry out the b...
Embodiment 2
[0025] The resin button components include 50 parts by weight of unsaturated polyester resin, 20 parts of calcium propionate, 10 parts of chitosan, 8 parts of glass fiber, 10 parts of microcrystalline wax, 8 parts of hollow glass microspheres, and 5 parts of curing agent. 6 parts, 6 parts of cobalt naphthalate, 10 parts of color paste, 8 parts of pearl powder and 10 parts of thixotropic agent.
[0026] The production technique of the present embodiment comprises the following steps:
[0027] A. Mix unsaturated polyester resin, calcium propionate, chitosan, glass fiber, microcrystalline wax, hollow glass microspheres, curing agent, cobalt naphthalate, color paste, pearl powder and thixotropic agent and add to the stirring tank Stir in medium, the stirring rate is 3000 rpm, and the stirring time is 20min, to obtain the mixture;
[0028] B, the mixing agent that step A obtains is added in the centrifuge barrel, adopts the bar casting method to make bar;
[0029] C, then carry o...
Embodiment 3
[0032] The resin button components include 35 parts by weight of unsaturated polyester resin, 12 parts of calcium propionate, 6 parts of chitosan, 3 parts of glass fiber, 3 parts of microcrystalline wax, 3 parts of hollow glass microspheres, and 2 parts of curing agent. 2 parts, 2 parts of cobalt naphthalate, 6 parts of color paste, 2 parts of pearl powder and 3 parts of thixotropic agent.
[0033] The production technique of the present embodiment comprises the following steps:
[0034] A. Mix unsaturated polyester resin, calcium propionate, chitosan, glass fiber, microcrystalline wax, hollow glass microspheres, curing agent, cobalt naphthalate, color paste, pearl powder and thixotropic agent and add to the stirring tank Stir in medium, the stirring rate is 1200 rpm, and the stirring time is 12min to obtain the mixture;
[0035] B, the mixing agent that step A obtains is added in the centrifuge barrel, adopts the bar casting method to make bar;
[0036] C, then carry out th...
PUM
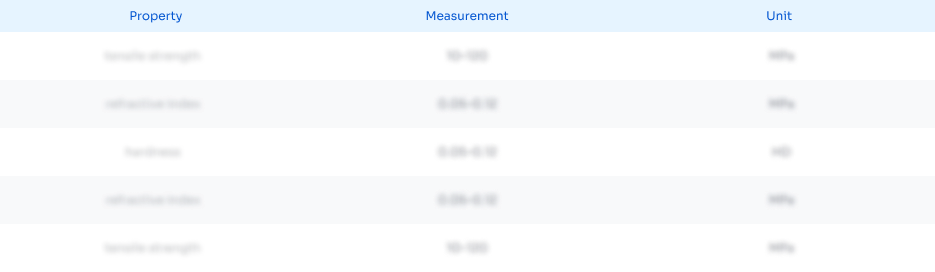
Abstract
Description
Claims
Application Information

- Generate Ideas
- Intellectual Property
- Life Sciences
- Materials
- Tech Scout
- Unparalleled Data Quality
- Higher Quality Content
- 60% Fewer Hallucinations
Browse by: Latest US Patents, China's latest patents, Technical Efficacy Thesaurus, Application Domain, Technology Topic, Popular Technical Reports.
© 2025 PatSnap. All rights reserved.Legal|Privacy policy|Modern Slavery Act Transparency Statement|Sitemap|About US| Contact US: help@patsnap.com