Preparation method of alpha-Fe2O3 nano laminated material and method for preparing benzaldehyde from material
A technology of nano-lamination and benzaldehyde, applied in the field of nano-materials, can solve the problems of difficult industrial application and unsatisfactory application effect, and achieve the effect of easy industrialization, good product performance and simple process
- Summary
- Abstract
- Description
- Claims
- Application Information
AI Technical Summary
Problems solved by technology
Method used
Image
Examples
Embodiment 1
[0039] Pre-mixing step: sequentially add 2 g of FeCl to 250 g of ethanol3 ·6H 2 O, 1.5 grams of deionized water and 1.5 grams of sodium acetate, stirred at 150 rpm for 45 minutes, reacted for 2 hours in a constant temperature water bath at 60° C., stopped stirring, and obtained a mixed solution.
[0040] Concentration step: Concentrate the mixed solution obtained in the pre-mixing step at 90° C. for 12 hours to obtain a concentrated solution.
[0041] Hydrothermal synthesis step: take 100 grams of the concentrated solution obtained in the concentration step and add it to a polytetrafluoroethylene-lined reactor, add 6 grams of deionized water and 8 grams of sodium acetate, stir at 150 rpm for 45 minutes, seal the kettle, and then React at 180°C for 8 hours, cool to room temperature after the reaction, centrifuge and filter, collect the solid product, wash with absolute ethanol and distilled water, and obtain α-Fe after drying 2 o 3 Nanolaminated materials.
Embodiment 2
[0043] Pre-mixing step: sequentially add 3 grams of FeCl to 250 grams of ethanol 3 ·6H 2 O, 1.5 grams of deionized water and 2 grams of sodium acetate, stirred at 200 rpm for 60 minutes, reacted in a constant temperature water bath at 70° C. for 1 hour, stopped stirring, and obtained a mixed solution.
[0044] Concentration step: the mixed liquid obtained in the pre-mixing step was concentrated at 95° C. for 6 hours to obtain a concentrated liquid.
[0045] Hydrothermal synthesis step: take 100 grams of the concentrated solution obtained in the concentration step and add it to a polytetrafluoroethylene-lined reactor, add 8 grams of deionized water and 10 grams of sodium acetate, stir at a rate of 200 rpm for 60 minutes, seal the kettle, and then React at 160°C for 12 hours, cool to room temperature after the reaction, centrifuge and filter, collect the solid product, wash with absolute ethanol and distilled water, and obtain α-Fe after drying 2 o 3 Nanolaminated materials. ...
Embodiment 3
[0047] Pre-mixing step: sequentially add 1 g of FeCl to 250 g of ethanol 3 ·6H 2 O, 1.5 grams of deionized water and 1 gram of sodium acetate, stirred at 100 rpm for 30 minutes, reacted in a constant temperature water bath at 45°C for 3 hours, stopped stirring, and obtained a mixed solution.
[0048] Concentration step: the mixed liquid obtained in the pre-mixing step was concentrated at 75° C. for 72 hours to obtain a concentrated liquid.
[0049] Hydrothermal synthesis step: take 100 grams of the concentrated solution obtained in the concentration step and add it to a polytetrafluoroethylene-lined reactor, add 5 grams of deionized water and 6 grams of sodium acetate, stir at a rate of 100 rpm for 30 minutes, seal the kettle, and then React at 200°C for 6 hours, cool to room temperature after the reaction, centrifuge and filter, collect the solid product, wash with absolute ethanol and distilled water, and obtain α-Fe after drying 2 o 3 Nanolaminated materials.
PUM
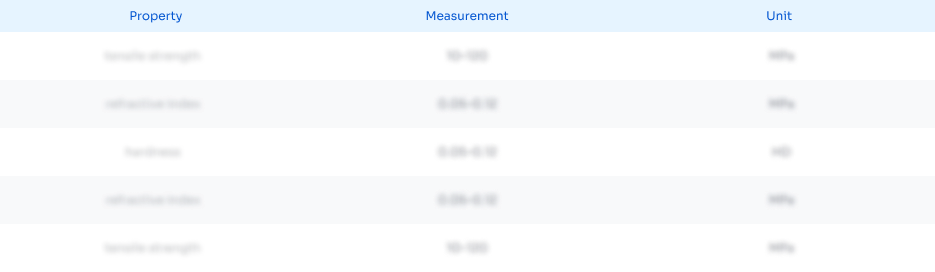
Abstract
Description
Claims
Application Information

- R&D
- Intellectual Property
- Life Sciences
- Materials
- Tech Scout
- Unparalleled Data Quality
- Higher Quality Content
- 60% Fewer Hallucinations
Browse by: Latest US Patents, China's latest patents, Technical Efficacy Thesaurus, Application Domain, Technology Topic, Popular Technical Reports.
© 2025 PatSnap. All rights reserved.Legal|Privacy policy|Modern Slavery Act Transparency Statement|Sitemap|About US| Contact US: help@patsnap.com