Foamed nickel-based NiCo2O4/MoS2 composite electrode material and preparation method thereof
A composite electrode and nickel foam technology, which is used in the manufacture of hybrid capacitor electrodes and hybrid/electric double-layer capacitors to achieve the effects of short reaction time, reduced energy consumption and reaction cost, and improved electrical conductivity
- Summary
- Abstract
- Description
- Claims
- Application Information
AI Technical Summary
Problems solved by technology
Method used
Image
Examples
Embodiment 1
[0027] Step 1: Weigh 0.2792g of nickel nitrate hexahydrate, 0.5588g of cobalt nitrate hexahydrate, 0.0592g of ammonium fluoride, and 0.2882g of urea and dissolve them in 20ml of deionized water to obtain solution A.
[0028] Step 2: Transfer solution A to a 20ml reactor and immerse the treated nickel foam in the solution, place it in a constant temperature oven at 110°C, and react at this temperature for 4 hours, wait for natural cooling to room temperature, and wash Dry to obtain sample A1;
[0029] Step 3: Transfer sample A1 to a square crucible, place the crucible in a muffle furnace, raise the muffle furnace to 320°C, and keep it at this temperature for 2h to obtain NiCo loaded on nickel foam 2 o 4 (NCO) samples.
Embodiment 2
[0031] Step 1: Weigh 0.2792g of nickel nitrate hexahydrate, 0.5588g of cobalt nitrate hexahydrate, 0.0592g of ammonium fluoride, and 0.2882g of urea and dissolve them in 20ml of deionized water to obtain solution A.
[0032] Step 2: Transfer solution A to a 20ml reactor and immerse the treated nickel foam in the solution, place it in a constant temperature oven at 110°C, and react at this temperature for 4 hours, wait for natural cooling to room temperature, and wash Dry to get sample A 1 ;
[0033] Step 3: Put sample A 1 Transfer to a square crucible, place the crucible in a muffle furnace, raise the muffle furnace to 320°C, and keep it at this temperature for 2h to obtain NiCo loaded on nickel foam 2 o 4 sample B;
[0034] Step 4: Dissolve 0.0177g ammonium molybdate and 0.0152g thiourea in 40ml deionized water to obtain solution C;
[0035] Step 5: Transfer solution C to a 50ml reactor and immerse sample B in the solution, place the reactor in a constant temperature ove...
Embodiment 3
[0037] Step 1: Weigh 0.2792g of nickel nitrate hexahydrate, 0.5588g of cobalt nitrate hexahydrate, 0.0592g of ammonium fluoride, and 0.2882g of urea and dissolve them in 20ml of deionized water to obtain solution A.
[0038] Step 2: Transfer solution A to a 20ml reactor and immerse the treated nickel foam in the solution, place it in a constant temperature oven at 110°C, and react at this temperature for 4 hours, wait for natural cooling to room temperature, and wash Dry to get sample A 1 ;
[0039] Step 3: Put sample A 1 Transfer to a square crucible, place the crucible in a muffle furnace, raise the muffle furnace to 320°C, and keep it at this temperature for 2h to obtain NiCo loaded on nickel foam 2 o 4 sample B;
[0040] Step 4: Weigh 0.0353g of ammonium molybdate and 0.0304g of thiourea and dissolve them in 40ml of deionized water to obtain solution C;
[0041] Step 5: Transfer solution C to a 50ml reactor and immerse sample B in the solution, place the reactor in a ...
PUM
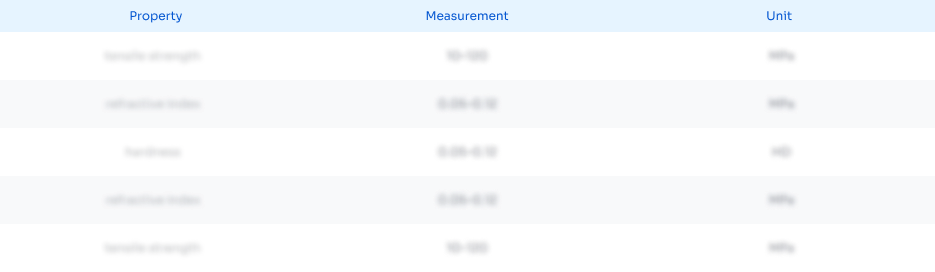
Abstract
Description
Claims
Application Information

- Generate Ideas
- Intellectual Property
- Life Sciences
- Materials
- Tech Scout
- Unparalleled Data Quality
- Higher Quality Content
- 60% Fewer Hallucinations
Browse by: Latest US Patents, China's latest patents, Technical Efficacy Thesaurus, Application Domain, Technology Topic, Popular Technical Reports.
© 2025 PatSnap. All rights reserved.Legal|Privacy policy|Modern Slavery Act Transparency Statement|Sitemap|About US| Contact US: help@patsnap.com