Self-cooling floating rolling-sliding composite bearing
A rolling-sliding composite bearing, floating type technology, applied in the direction of rotating combined bearings, rotating bearings, bearings, etc., can solve the problems of large friction coefficient of bearing friction pairs, increased wear speed of the drill bit to the bearing, and unsuitable problems, so as to achieve improvement The ability to resist high load, strong impact and high speed, improve rock breaking efficiency, and not easy to deteriorate
- Summary
- Abstract
- Description
- Claims
- Application Information
AI Technical Summary
Problems solved by technology
Method used
Image
Examples
Embodiment Construction
[0028] In order for those skilled in the art to better understand the present invention, the present invention will be further described in detail below in conjunction with the accompanying drawings and the following embodiments.
[0029] Such as figure 1 with image 3 As shown, this embodiment provides a self-cooling floating type rolling-sliding composite bearing. The rolling-sliding composite bearing 1 is used to install a detachably connected broken drill bit 7 at the core of the drill bit, which can realize the detachable installation of the broken drill bit 7 at the center of the drill bit. part or integrally connected at the core of the drill bit to improve the rock-breaking efficiency of the core of the drill bit and adapt to breaking through harder formations; the rolling-slip composite bearing 1 includes the inner rotator 2, the outer rotator 3 and the inner rotator 2 and the outer rotator The ring-shaped installation groove 4 formed between the bodies 3, 8 rolling ...
PUM
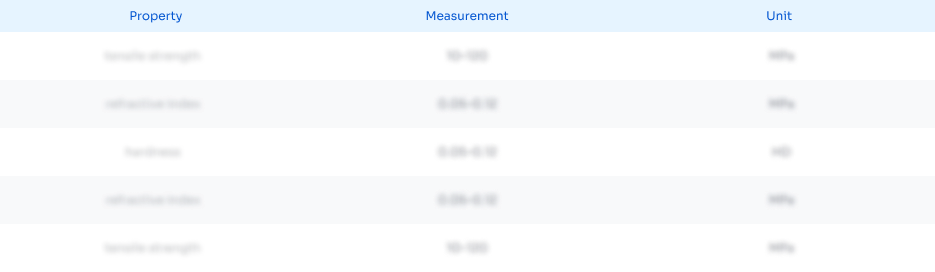
Abstract
Description
Claims
Application Information

- R&D Engineer
- R&D Manager
- IP Professional
- Industry Leading Data Capabilities
- Powerful AI technology
- Patent DNA Extraction
Browse by: Latest US Patents, China's latest patents, Technical Efficacy Thesaurus, Application Domain, Technology Topic, Popular Technical Reports.
© 2024 PatSnap. All rights reserved.Legal|Privacy policy|Modern Slavery Act Transparency Statement|Sitemap|About US| Contact US: help@patsnap.com