Boron bearing steel smelting technological method for improving boron yield
A process method and a technology of yield rate, applied in the field of boron-containing steel smelting process, can solve problems such as short boron elements, achieve the effects of increasing the content, reducing production costs, and shortening the smelting process
- Summary
- Abstract
- Description
- Claims
- Application Information
AI Technical Summary
Problems solved by technology
Method used
Examples
Embodiment 1
[0032] 1) High-temperature tapping of the converter, the tapping temperature reaches 1668°C, about 30% of the tapping is added to molten steel for deoxidation and alloying; after tapping, add slag adjustment to the slag surface of the ladle The agent is 3.3kg / t, the particle size of the slagging agent is 60mm, and the composition is: Al 39%, Ca 8%, CaO 30%, Al 2 o 3 16%, CaF 2 6%, the rest is impurities, lime 2.6kg / t, the flow rate of argon gas blowing at the bottom of the ladle during tapping is controlled at 150NL / min, and the bottom blowing and stirring are continued for 4.5 minutes after all the alloy and slag adjusting agent are added;
[0033] 2) The ladle is transferred to the VOD station, the VOD entry temperature is 1617°C, and the T.Fe+MnO is 1.76%. After the ladle is placed in place, turn on the bottom blowing and start vacuuming. The flow rate of the bottom blowing argon and hydrogen gas mixture is 15NL / min, the capacity ratio of argon to hydrogen is 8:2, and t...
Embodiment 2
[0036] 1) High-temperature tapping of the converter, the tapping temperature reaches 1675°C, about 30% of the tapping is added to the molten steel for deoxidation alloying, such as aluminum, ferrosilicon, manganese alloy, carbon powder, etc.; after tapping, add slag adjustment to the ladle slag surface The agent is 1.5kg / t, the particle size of the slagging agent is 40mm, and the composition is: Al 30%, Ca 10%, CaO 35%, Al 2 o 3 15%, CaF 2 5%, the rest is impurities, lime 2.0kg / t, the flow rate of argon gas blowing at the bottom of the ladle during tapping is controlled at 80NL / min, and the bottom blowing and stirring are continued for 4 minutes after all the alloy and slag adjusting agent are added;
[0037]2) The ladle is transferred to the VOD station, the VOD entry temperature is 1615°C, and the T.Fe+MnO is 1.55%. After the ladle is placed in place, turn on the bottom blowing and start vacuuming. The flow rate of the bottom blowing argon and hydrogen gas mixture is 5NL...
Embodiment 3
[0040] 1) High-temperature tapping of the converter, the tapping temperature reaches 1655°C, about 30% of the tapping is added to the molten steel for deoxidation and alloying; after tapping, add slag adjustment to the slag surface of the ladle The agent is 5.5kg / t, the particle size of the slagging agent is 70mm, and the composition is: Al 40%, Ca 3%, CaO 25%, Al 2 o 3 20%, CaF 2 10%, the rest is impurities, lime 4.0kg / t, the flow rate of argon gas blowing at the bottom of the ladle during tapping is controlled at 200NL / min, and the bottom blowing and stirring are continued for 3.8 minutes after all the alloy and slag adjusting agent are added;
[0041] 2) The ladle is transferred to the VOD station, the VOD entry temperature is 1625°C, and the T.Fe+MnO is 2.00%. After the ladle is placed in place, turn on the bottom blowing and start vacuuming. The flow rate of the bottom blowing argon and hydrogen gas mixture is 50NL / min, the capacity ratio of argon to hydrogen is 9:1, ...
PUM
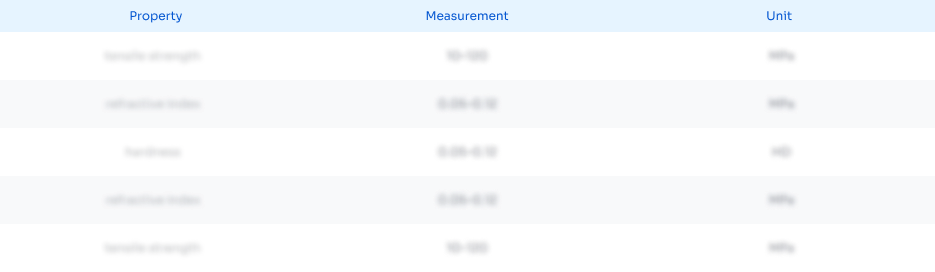
Abstract
Description
Claims
Application Information

- Generate Ideas
- Intellectual Property
- Life Sciences
- Materials
- Tech Scout
- Unparalleled Data Quality
- Higher Quality Content
- 60% Fewer Hallucinations
Browse by: Latest US Patents, China's latest patents, Technical Efficacy Thesaurus, Application Domain, Technology Topic, Popular Technical Reports.
© 2025 PatSnap. All rights reserved.Legal|Privacy policy|Modern Slavery Act Transparency Statement|Sitemap|About US| Contact US: help@patsnap.com