Electromagnetic positioning vibration isolation platform
A vibration isolation platform and electromagnetic positioning technology, which is applied to aerospace equipment, aerospace vehicles, aircraft, etc., can solve the problems of inability to measure and control micro-vibration acceleration, and complex installation of measuring components.
- Summary
- Abstract
- Description
- Claims
- Application Information
AI Technical Summary
Problems solved by technology
Method used
Image
Examples
Embodiment 1
[0034] Such as figure 1 and 2 The electromagnetic positioning vibration isolation platform shown has a base 2, a working platform 1, a force output system, an acceleration measurement unit, a position measurement unit and a controller; the force output system is composed of 3 sets of two-axis electromagnetic exciters, The two-axis electromagnetic exciter connects the working platform 1 and the base 2 without contact through the Lorentz force, and the two-axis electromagnetic exciter is arranged in a uniform array along the same circle at 120° with the center of the working platform 1 as the center; the acceleration measurement unit consists of 6 The linear acceleration sensor 4-2 is formed, and every two linear acceleration sensors are installed orthogonally on an acceleration sensor installation block 4-1, and the acceleration sensor installation block 4-1 is fixed with the working platform 1, and the center of the working platform 1 is the center of the circle along the Th...
Embodiment 2
[0050] The difference between this embodiment and Embodiment 1 lies in that the coils are wound in different ways. The rest of the structure is the same as that of Embodiment 1 except for the coil.
[0051] The specific structure of the coil is as follows: Figure 3-2 -1 and 3-2-2, the coil contains x to the coil set 112 and z To the coil set 122, x to the coil set 112 and z The directional coil group 122 is formed by respective first sub-coils and second sub-coils, the first sub-coils and the second sub-coils are adjacent and wound by a wire, the first sub-coils are wound counterclockwise from inside to outside, and the second sub-coils are wound from inside to outside. The second sub-coil is wound clockwise from the outside to the inside, the first sub-coil and the second sub-coil are in the same plane, the first sub-coil and the second sub-coil are respectively wound with multiple turns, and each turn is composed of an effective wire segment and a connecting wire segme...
Embodiment 3
[0054] The difference between this embodiment and Embodiment 1 lies in that the coils are wound in different ways. The rest of the structure is the same as that of Embodiment 1 except for the coil.
[0055] The specific structure of the coil is as follows: Figure 3-3 shown, the coil contains x to coil 123 and z to the coil 113, x In the coil 123, the multi-turn wire segments that are located in the working magnetic field shown by the dotted line box are equidistantly distributed to form z To the Lorentz force generation department, x The wire segment located outside the working magnetic field to the coil 123 is used as the connecting wire segment; z To the equidistant distribution of multi-turn wire segments in the magnetic field in the coil 113 is formed x To the Lorentz force generation department, z The conductor segments lying outside the magnetic field to the coil 113 serve as connecting conductor segments. to produce perpendicular x Lorentz force sum z to the ...
PUM
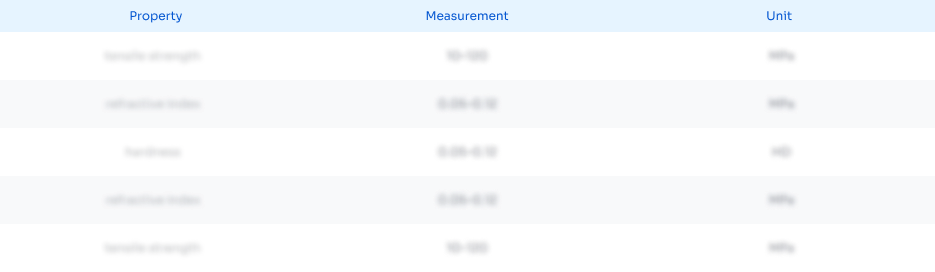
Abstract
Description
Claims
Application Information

- R&D
- Intellectual Property
- Life Sciences
- Materials
- Tech Scout
- Unparalleled Data Quality
- Higher Quality Content
- 60% Fewer Hallucinations
Browse by: Latest US Patents, China's latest patents, Technical Efficacy Thesaurus, Application Domain, Technology Topic, Popular Technical Reports.
© 2025 PatSnap. All rights reserved.Legal|Privacy policy|Modern Slavery Act Transparency Statement|Sitemap|About US| Contact US: help@patsnap.com