Glass spray painting process and system
A spray painting and glass technology, applied in the field of spray painting, can solve the problems of pattern deviation, difficult pattern positioning, low pattern size accuracy and position accuracy, and achieve the effect of reducing size deviation
- Summary
- Abstract
- Description
- Claims
- Application Information
AI Technical Summary
Problems solved by technology
Method used
Image
Examples
Embodiment 1
[0034] Such as figure 1 and 2As shown, a glass inkjet system includes a preheating zone, a heat preservation zone, a printing zone and a conveying platform 100. The glass plate is placed on the conveying platform 100, and the conveying platform 100 can drive the glass plate to pass through the preheating zone, the heat preservation zone and the conveying platform in sequence. The printing area, the preheating area and the heat preservation area can respectively carry out preheat treatment and heat preservation treatment on the glass plate in sequence. An ink storage unit 200, an inkjet unit 300 and a heating unit 400 are installed on the printing area. Car 310, spray car 310 can move left and right and longitudinally on the conveying direction of conveying platform 100, the spray head 311 that is used for inkjet painting is installed on the spray car 310, ink storage unit 200 can deliver ink to print head 311, and heating unit 400 is installed on On the spraying vehicle 310 ...
Embodiment 2
[0042] The difference between this embodiment and embodiment 1 is that silicate and organic solvent are dissolved in the ink, and the silicate is sodium silicate. Others are the same as embodiment 1.
Embodiment 3
[0044] The difference between this embodiment and embodiment 2 is that the silicate is calcium silicate. Others are the same as embodiment 2.
PUM
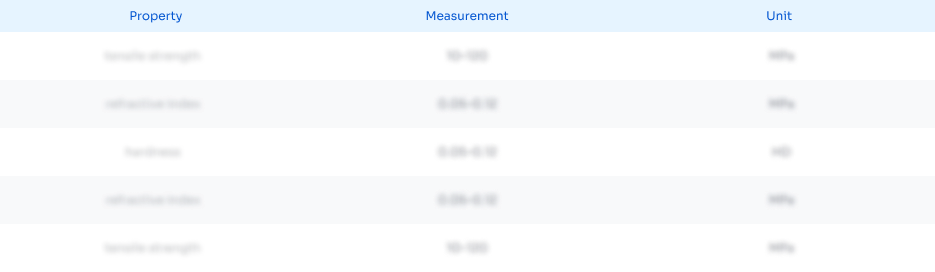
Abstract
Description
Claims
Application Information

- R&D
- Intellectual Property
- Life Sciences
- Materials
- Tech Scout
- Unparalleled Data Quality
- Higher Quality Content
- 60% Fewer Hallucinations
Browse by: Latest US Patents, China's latest patents, Technical Efficacy Thesaurus, Application Domain, Technology Topic, Popular Technical Reports.
© 2025 PatSnap. All rights reserved.Legal|Privacy policy|Modern Slavery Act Transparency Statement|Sitemap|About US| Contact US: help@patsnap.com