Cold straightening process for puncher
A puncher and process technology, applied in the field of calibration technology, can solve the problems that the calibration accuracy cannot be effectively controlled, affect the quality and service life of the product, and affect the hardness of the puncher product, etc., to solve the beating, ensure the hardness, avoid damage effect
- Summary
- Abstract
- Description
- Claims
- Application Information
AI Technical Summary
Problems solved by technology
Method used
Image
Examples
Embodiment Construction
[0013] The present invention will be further described in detail below in conjunction with the accompanying drawings and specific embodiments.
[0014] Such as figure 1 Shown, overall steps of the present invention are as follows:
[0015] Step 1. Fixing the workpiece: Start the open switch of the pneumatic chuck 1, the pressure of the gas will decrease after passing through the pressure reducing valve 2 on the rear side of the pneumatic chuck 1, and the jaws of the pneumatic chuck 1 will be released in the direction away from the puncher 3; The hexagonal end of the punch 3 is inserted into the pneumatic chuck 1; the closing switch of the pneumatic chuck 1 is activated, the pressure increases after the gas comes out through the booster valve 4, and the claws of the pneumatic chuck 1 are pushed toward the punch 3 to clamp;
[0016] Step 2. Find the out-of-range point: install the dial gauge 5 on the highest part of the outer circle of the puncher 3 by rotating the dial stand; ...
PUM
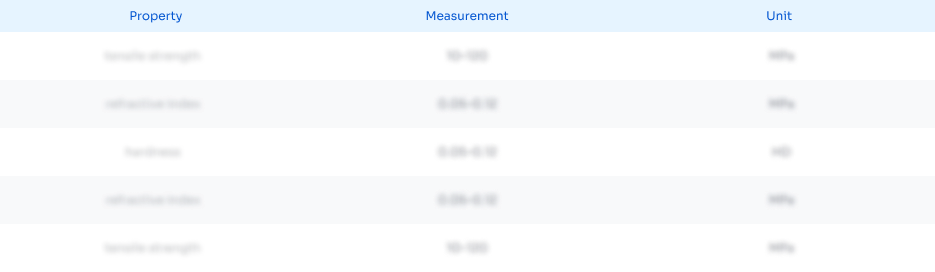
Abstract
Description
Claims
Application Information

- R&D
- Intellectual Property
- Life Sciences
- Materials
- Tech Scout
- Unparalleled Data Quality
- Higher Quality Content
- 60% Fewer Hallucinations
Browse by: Latest US Patents, China's latest patents, Technical Efficacy Thesaurus, Application Domain, Technology Topic, Popular Technical Reports.
© 2025 PatSnap. All rights reserved.Legal|Privacy policy|Modern Slavery Act Transparency Statement|Sitemap|About US| Contact US: help@patsnap.com