Molding material
A molding material and component technology, applied in the field of materials, can solve problems such as easy cracking, low compressive strength, leakage, etc., and achieve the effect of promoting plasticization, enhancing hardness, and not easy to crack
- Summary
- Abstract
- Description
- Claims
- Application Information
AI Technical Summary
Problems solved by technology
Method used
Examples
Embodiment 1
[0023] (1) Wet mixing: put 3.5 parts of carbon nanotubes into 60 parts of ethanol and sonicate for 45 min, put 51 parts of polytetrafluoroethylene into the solution after sonication, stir at high speed for 30 min, and then put the stirred solution into Ultrasonic for 1 h in an ultrasonic cleaner, dried in a blast drying oven, and set aside.
[0024] (2) Under the action of ultrasound, disperse the substance prepared in step (1) into 25 parts of xylene, then add 95 parts of high-density polyvinyl chloride at 158 ° C, stir until it is completely dissolved, and then add the Stir 2 parts of methyl methacrylate and ethyl acrylate copolymer (the mass ratio of methyl methacrylate and ethyl acrylate is 5:2), then add 25 parts of calcium carbonate, 5 parts of chlorinated polyethylene, and 0.5 parts of polyethylene wax 5 parts, 0.5 parts of stearic acid, 4 parts of cerium chloride, mix evenly and slowly pour the mixed solution into a large amount of absolute ethanol to stir and floccu...
Embodiment 2
[0026] (1) Wet mixing: Put 2 parts of carbon nanotubes into 60 parts of ethanol and sonicate for 45 min, put 60 parts of polytetrafluoroethylene into the solution after sonication, stir at high speed for 30 min, and then put the stirred solution into Ultrasonic for 1 h in an ultrasonic cleaner, dried in a blast drying oven, and set aside.
[0027] (2) Under the action of ultrasound, disperse the substance prepared in step (1) into 25 parts of xylene, then add and stir at 158 °C until it is completely dissolved, then add methyl methacrylate and ethyl acrylate Stir 1.5 parts of copolymer (methyl methacrylate, ethyl acrylate mass ratio is 5:4), then add 25 parts of calcium carbonate, 12 parts of chlorinated polyethylene, 2.1 parts of polyethylene wax, 0.7 parts of stearic acid, chlorine 3-5 parts of cerium oxide, mix evenly, slowly pour the mixed liquid into a large amount of absolute ethanol, stir and flocculate, filter, dry, and powder to obtain a composite injection molding ...
Embodiment 3
[0029] (1) Wet mixing: put 5 parts of carbon nanotubes into 60 parts of ethanol and sonicate for 45 min, put 48 parts of polytetrafluoroethylene into the ultrasonic solution, stir at high speed for 30 min, and then put the stirred solution into Ultrasonic for 1 h in an ultrasonic cleaner, dried in a blast drying oven, and set aside.
[0030] (2) Under the action of ultrasound, disperse the substance prepared in step (1) into 25 parts of xylene, then add and stir at 158 °C until it is completely dissolved, then add methyl methacrylate and ethyl acrylate Stir 3 parts of copolymer, then add 33 parts of calcium carbonate, 7 parts of chlorinated polyethylene, 0.5 parts of polyethylene wax, 1.9 parts of stearic acid, 3~5 parts of lanthanum oxide, mix well and slowly pour the mixture into a large amount of Stir and flocculate in absolute ethanol, filter, dry, and powder to obtain a composite injection molding material. The obtained masterbatch and high-density polyvinyl chloride p...
PUM
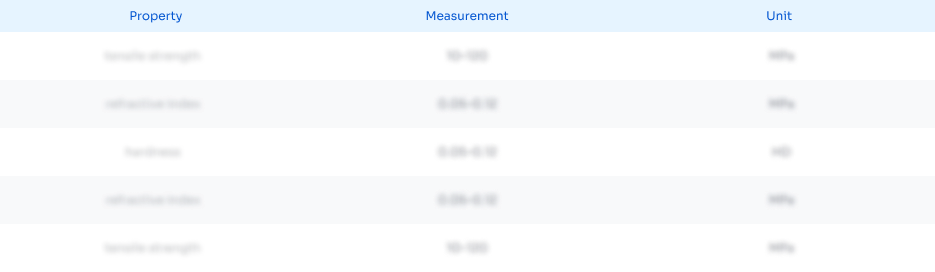
Abstract
Description
Claims
Application Information

- R&D
- Intellectual Property
- Life Sciences
- Materials
- Tech Scout
- Unparalleled Data Quality
- Higher Quality Content
- 60% Fewer Hallucinations
Browse by: Latest US Patents, China's latest patents, Technical Efficacy Thesaurus, Application Domain, Technology Topic, Popular Technical Reports.
© 2025 PatSnap. All rights reserved.Legal|Privacy policy|Modern Slavery Act Transparency Statement|Sitemap|About US| Contact US: help@patsnap.com