Nano-ceramic polymer heavy-anticorrosion coating and preparation method thereof
A nano-ceramic and polymer technology, applied in anti-corrosion coatings, fire-resistant coatings, polyurea/polyurethane coatings, etc., can solve the problems of low-zinc type epoxy zinc-rich paint anti-corrosion effect, not ideal, etc., to achieve good metal anti-corrosion Function, good heat insulation effect, convenient construction
- Summary
- Abstract
- Description
- Claims
- Application Information
AI Technical Summary
Problems solved by technology
Method used
Image
Examples
Embodiment 1
[0024] A nano-ceramic polymer heavy-duty anti-corrosion coating, its components are composed of the following parts by weight: 30g polyurethane prepolymer, 15g modified acrylate, 10g polyaniline, 30g composite powder, 15g epoxy resin, 20g nano ceramics, 6g zirconia, 3g yttrium oxide, 7g glass wool, 1g porcelain powder, 6g kaolin, 5g mica powder, 8g zinc powder, 2g titanium dioxide and 0.5g silicon defoamer.
[0025] Wherein, described polyurethane prepolymer preparation method is:
[0026] (1) Add 80g of polyether diol into the reaction kettle, set the temperature of the oil bath heating device to 110°C, turn on the vacuum pump, turn on the stirring device after the vacuum degree reaches -0.09MPa, and dehydrate for 4 hours;
[0027] (2) Add 0.002g, 98wt% concentrated phosphoric acid to the reactor, keep a vacuum degree of -0.09MPa and a stirring state, turn off the oil bath heating device, turn on the condensed water to reduce the temperature in the reactor to 45±5°C, and stop...
Embodiment 2
[0036] A nano-ceramic polymer heavy-duty anti-corrosion coating, its components are composed of the following parts by weight: 35g polyurethane prepolymer, 20g modified acrylate, 13g polyaniline, 20g composite powder, 10g epoxy resin, 15g nano ceramics, 10g zirconia, 6g yttrium oxide, 5g glass wool, 3g porcelain powder, 1g kaolin, 1g mica powder, 12g zinc powder, 4g carbon black and 0.8g silicon defoamer.
[0037] Wherein, described polyurethane prepolymer preparation method is:
[0038] (1) Add 90g of polyether diol into the reaction kettle, set the temperature of the oil bath heating device to 110°C, turn on the vacuum pump, turn on the stirring device after the vacuum degree reaches -0.09MPa, and dehydrate for 4 hours;
[0039] (2) Add 0.004g, 98wt% concentrated phosphoric acid to the reactor, keep the vacuum degree and stirring state of -0.09MPa, turn off the oil bath heating device, turn on the condensed water, reduce the temperature in the reactor to 45±5°C, and stop sti...
Embodiment 3
[0048] A nano-ceramic polymer heavy-duty anti-corrosion coating, its components are composed of the following parts by weight: 40g polyurethane prepolymer, 25g modified acrylate, 16g polyaniline, 50g composite powder, 13g epoxy resin, 25g nano ceramics, 8g zirconia, 4g yttrium oxide, 8g glass wool, 6g porcelain powder, 10g kaolin, 8g mica powder, 10g zinc powder, 5g iron oxide red and 1g silicon defoamer.
[0049] Wherein, described polyurethane prepolymer preparation method is:
[0050] (1) Add 85g of polyether diol into the reaction kettle, set the temperature of the oil bath heating device to 110°C, turn on the vacuum pump, turn on the stirring device after the vacuum degree reaches -0.09MPa, and dehydrate for 4 hours;
[0051] (2) Add 0.005g, 98wt% concentrated phosphoric acid to the reaction kettle, keep the vacuum degree of -0.09MPa and stirring state, turn off the oil bath heating device, turn on the condensate water to reduce the temperature in the reaction kettle to 4...
PUM
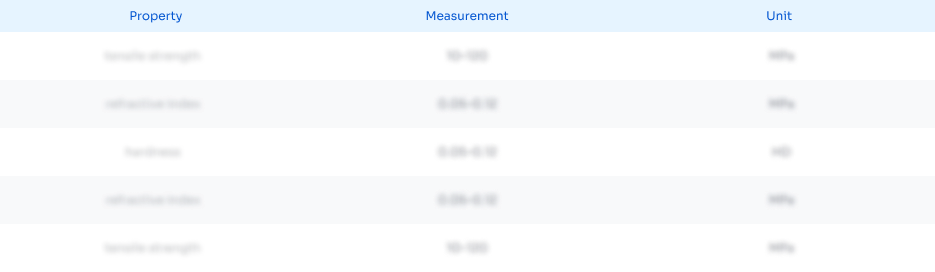
Abstract
Description
Claims
Application Information

- R&D
- Intellectual Property
- Life Sciences
- Materials
- Tech Scout
- Unparalleled Data Quality
- Higher Quality Content
- 60% Fewer Hallucinations
Browse by: Latest US Patents, China's latest patents, Technical Efficacy Thesaurus, Application Domain, Technology Topic, Popular Technical Reports.
© 2025 PatSnap. All rights reserved.Legal|Privacy policy|Modern Slavery Act Transparency Statement|Sitemap|About US| Contact US: help@patsnap.com