Epoxy curing agent taking bark as raw material and preparation method thereof
A technology of epoxy curing agent and bark, which is applied in the field of epoxy curing agent and its preparation, can solve the problems of low bark utilization level, and achieve the effect of promoting high value-added utilization, simple extraction, and low energy consumption
- Summary
- Abstract
- Description
- Claims
- Application Information
AI Technical Summary
Problems solved by technology
Method used
Examples
Embodiment 1
[0015] In the first step, the American black pine bark is dried and crushed, and then passed through a 40-mesh sieve to obtain bark powder. After mixing the bark powder with NaOH and water in a weight ratio of 1:9:90, keep the temperature at 95°C for 3 hour, filter the residue, and obtain the bark extract after the liquid is spray-dried.
[0016] In the second step, 90g of bark extract, 900g of epichlorohydrin, 900g of 1,4-dioxane and 0.5g of benzyltriethylammonium chloride are added to a tank equipped with a mechanical stirring blade, a thermometer and a reflux condenser. In a three-necked flask, heat up to 75°C and stir thoroughly for 6 hours, then lower the temperature to 60°C, add 20g of sodium hydroxide and 12g of calcium oxide, stir for 9 hours, add 500mL of acetone to the mixture to dilute, then filter to remove solid salt, and then add acetone and excess After the epichlorohydrin is reclaimed by vacuum distillation, a kind of bark powder source epoxy compound (Bark-epo...
Embodiment 2
[0018] In the first step, the bark of the masson pine bark is dried and crushed and sieved through a 40-mesh sieve to obtain the bark powder. After mixing the bark powder with KOH and water in a weight ratio of 1:10:100, keep the temperature at 100°C for 3 hours , filter the residue, and obtain the bark extract after the liquid is spray-dried.
[0019] In the second step, in a 500mL three-necked flask equipped with a mechanical stirrer, a water separator and a thermometer, add 4.6g of bark extract and 6.5g of aminoethylpiperazine and mix evenly, then raise the temperature to 80°C, and dissolve 12g of 37% formaldehyde solution was added dropwise, and after 6 hours of reaction, the temperature was raised to 120°C to collect excess water in the water separator to obtain a Mannich base curing agent.
Embodiment 3
[0021] In the first step, the Korean pine bark is sun-dried and crushed and sieved through a 40-mesh sieve to obtain the bark powder. After mixing the bark powder and ethylenediamine in a weight ratio of 1:15, keep the temperature at 95°C for 3 hours, and filter The residue, the liquid is spray dried to obtain the bark extract.
[0022] In the second step, 90g of bark extract, 900g of epichlorohydrin, 900g of 1,4-dioxane and 12.5mL of tetrabutylammonium hydroxide were added in a three-necked flask equipped with a mechanical stirring paddle, a thermometer and a reflux condenser, After raising the temperature to 60°C, fully stir for 7 hours, then lower the temperature to 60°C, add 40g of sodium hydroxide and 1g of calcium oxide, and stir for 5 hours, add 500mL of acetone to the mixture to dilute, then filter to remove solid salt, then add acetone and excess epoxy chlorine After the propane is recovered by distillation under reduced pressure, a kind of bark powder source epoxy co...
PUM
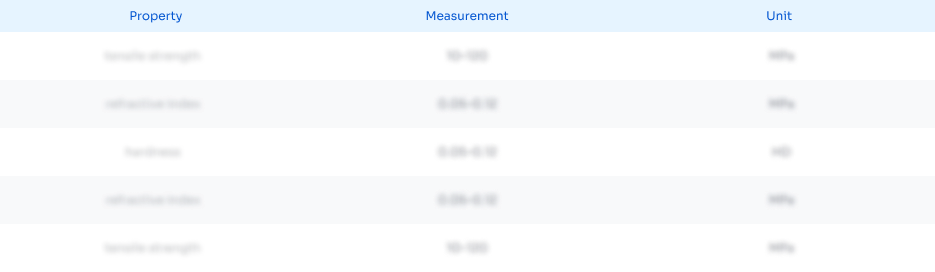
Abstract
Description
Claims
Application Information

- R&D
- Intellectual Property
- Life Sciences
- Materials
- Tech Scout
- Unparalleled Data Quality
- Higher Quality Content
- 60% Fewer Hallucinations
Browse by: Latest US Patents, China's latest patents, Technical Efficacy Thesaurus, Application Domain, Technology Topic, Popular Technical Reports.
© 2025 PatSnap. All rights reserved.Legal|Privacy policy|Modern Slavery Act Transparency Statement|Sitemap|About US| Contact US: help@patsnap.com