Ceramizable polymer material having self-supporting performance and preparation method thereof
A technology of polymer materials and ceramics, applied in the direction of organic insulators, plastic/resin/wax insulators, rubber insulators, etc., can solve the problems of material softening and deformation, high cost, fracture loss, etc., to improve self-supporting performance and bending strength , good self-supporting performance, excellent self-supporting performance
- Summary
- Abstract
- Description
- Claims
- Application Information
AI Technical Summary
Problems solved by technology
Method used
Image
Examples
Embodiment 1
[0032] Raw material quality ratio:
[0033]
[0034] First, add silicate glass powder and phosphate compound into a high-speed mixer, stir at high speed for 20 minutes to form a mixed powder, and take it out for later use. Then pour the ethylene-vinyl acetate copolymer into a two-roll plastic mill, keep the temperature at 85°C and cut for 2 minutes, so that the organic polymer can wrap the front roll; then slowly add the mixed powder to be used, and mix with ethylene- The vinyl acetate copolymer was mixed for 12 minutes until the mixed powder and the base material were evenly mixed. The sheet obtained by kneading was hot-pressed on a flat vulcanizer, the temperature was set at 170°C, pressed at 10MPa for 20min, and then cold-pressed, the cold-pressing time was 5min, and the pressure was 10MPa.
[0035] The performance test results are shown in Table 1.
Embodiment 2
[0037] Raw material quality ratio:
[0038]
[0039]First, add silicate glass powder and phosphate compound into the high-speed mixer, stir at high speed for 20 minutes, and take it out for later use. Then pour the ethylene-vinyl acetate copolymer into a two-roll plastic mill, keep the temperature at 85°C and shear for 2 minutes, so that the organic polymer matrix can wrap the front roll, and then gradually add the above-mentioned mixed silicic acid for use The salt glass powder and the phosphate compound powder are mixed with the matrix, and the mixing time is 12 minutes until the powder and the matrix material are evenly mixed. The sheet obtained by kneading was hot-pressed on a flat vulcanizer, the temperature was set at 170°C, and pressed at 10 MPa for 15 minutes, and then cold-pressed, the cold-pressing time was 5 minutes, and the pressure was 10 MPa.
[0040] The performance test results are shown in Table 2.
Embodiment 3
[0042] Raw material quality ratio:
[0043]
[0044] First, add silicate glass powder and phosphate compound into the high-speed mixer, stir at high speed for 20 minutes, and take it out for later use. Then pour the ethylene-vinyl acetate copolymer into a two-roll plastic mill, keep the temperature at 85°C and shear for 2 minutes, so that the organic polymer matrix can wrap the front roll, and then gradually add the above-mentioned mixed silicic acid for use Salt glass powder and phosphate compound are mixed with the matrix for 12 minutes until the powder and the matrix material are evenly mixed. When hot-pressing the kneaded sheets on a flat vulcanizer, set the temperature at 170°C and press at 10 MPa for 15 minutes, and then perform cold pressing for 5 minutes at a pressure of 10 MPa.
[0045] The performance test results are shown in Table 3.
PUM
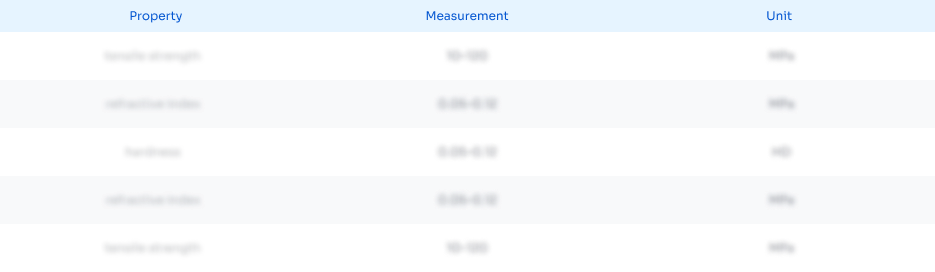
Abstract
Description
Claims
Application Information

- R&D
- Intellectual Property
- Life Sciences
- Materials
- Tech Scout
- Unparalleled Data Quality
- Higher Quality Content
- 60% Fewer Hallucinations
Browse by: Latest US Patents, China's latest patents, Technical Efficacy Thesaurus, Application Domain, Technology Topic, Popular Technical Reports.
© 2025 PatSnap. All rights reserved.Legal|Privacy policy|Modern Slavery Act Transparency Statement|Sitemap|About US| Contact US: help@patsnap.com