Production technique for mass polyvinyl chloride
A polyvinyl chloride, production process technology, applied in the field of vinyl chloride polymerization reaction process, can solve the problems of many batches of pressure fluctuations, low rate of high-quality products, high rate of B-grade products, etc., to reduce the rate of B-grade products, reduce The effect of product agglomeration and internal quality improvement
- Summary
- Abstract
- Description
- Claims
- Application Information
AI Technical Summary
Problems solved by technology
Method used
Image
Examples
Embodiment 1
[0043] Bulk polyvinyl chloride type 7 resin is produced as follows:
[0044] (1) After the pre-polymerization tank completes the vacuum replacement, the liquid vinyl chloride monomer is transported into the pre-polymerization tank with a monomer pump. The temperature is as high as 68°C, and the pressure is 1.2MPa, and the pre-polymerization reaction is carried out, and the "seed" is obtained after 15 minutes of reaction.
[0045] (2) Add 3000g of polymerization aid antioxidant 2,6-di-tert-butyl-p-cresol and 200g of polymerization aid thickener crotonic acid, ethyl acetate copolymer and 2L of nitric acid solution with a mass concentration of 20% In the polymerization kettle, the polymerization kettle is vacuum replaced; then 15t of vinyl chloride monomer is added to the polymerization kettle, and the "seed" obtained in step (1) is added, and the initiator EHPD of 0.04% of the total mass of the vinyl chloride monomer is added and 0.007% initiator Luperox 701M70, then pass hot w...
Embodiment 2
[0048] Bulk polyvinyl chloride type 7 resin is produced as follows:
[0049](1) After the pre-polymerization tank completes the vacuum replacement, the liquid vinyl chloride monomer is transported into the pre-polymerization tank with a monomer pump. The temperature is as high as 68°C, and the pressure is 1.2MPa, and the pre-polymerization reaction is carried out, and the "seed" is obtained after 15 minutes of reaction.
[0050] (2) 2800g polymerization aid antioxidant 2,6-di-tert-butyl p-cresol and 186g polymerization aid thickener crotonic acid, ethyl acetate copolymer and 1.8L mass concentration are 20% nitric acid solution together Put into the polymerization kettle, and vacuum replace the polymerization kettle; then add 14.5t vinyl chloride monomer to the polymerization kettle, and add the "seed" obtained in step (1), and then add 0.04% of the total mass of vinyl chloride monomer to initiate agent EHPD and 0.007% initiator Luperox 701M70, and then pass hot water at 80°C ...
PUM
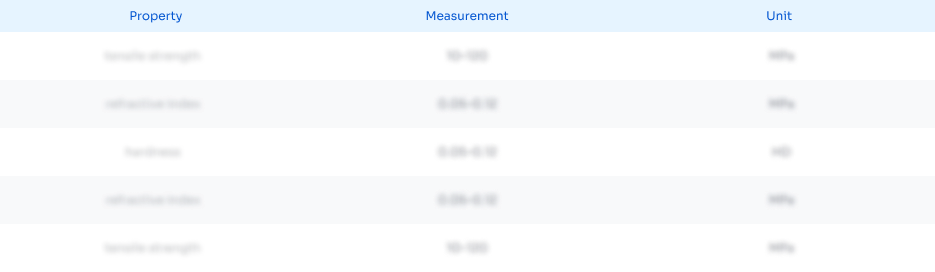
Abstract
Description
Claims
Application Information

- R&D
- Intellectual Property
- Life Sciences
- Materials
- Tech Scout
- Unparalleled Data Quality
- Higher Quality Content
- 60% Fewer Hallucinations
Browse by: Latest US Patents, China's latest patents, Technical Efficacy Thesaurus, Application Domain, Technology Topic, Popular Technical Reports.
© 2025 PatSnap. All rights reserved.Legal|Privacy policy|Modern Slavery Act Transparency Statement|Sitemap|About US| Contact US: help@patsnap.com