Machining and additive manufacturing combined water turbine model rotating wheel manufacturing method
A water turbine model and mechanical processing technology, applied in teaching models, manufacturing tools, additive processing, etc., can solve the problems of large surface fluctuations of parts and low surface quality of formed parts, and achieve high processing accuracy, low cost, and short cycle Effect
- Summary
- Abstract
- Description
- Claims
- Application Information
AI Technical Summary
Problems solved by technology
Method used
Image
Examples
Embodiment Construction
[0023] The present invention will be further described below in conjunction with accompanying drawing and specific embodiment:
[0024] As shown in Figure 1, the blanking of the upper crown 1 is carried out, the material is 304 austenitic stainless steel plate, and the manufacturing of the upper crown 1 is completed by mechanical processing after blanking;
[0025] As shown in Figure 2, the blanking of the lower ring 3 is carried out, the material is 304 austenitic stainless steel plate, and the manufacturing of the lower ring 3 is completed by machining after blanking;
[0026] As shown in Figure 3, the three-dimensional mathematical model of the turbine model runner is imported into the special software, and the flow surface of the upper crown 1 is used as the basis for additive manufacturing, and the relative position of each blade 2 on the upper crown 1 is determined, and the flow of the blade 2 is determined. The machining allowance of 2.0mm is automatically added to the ...
PUM
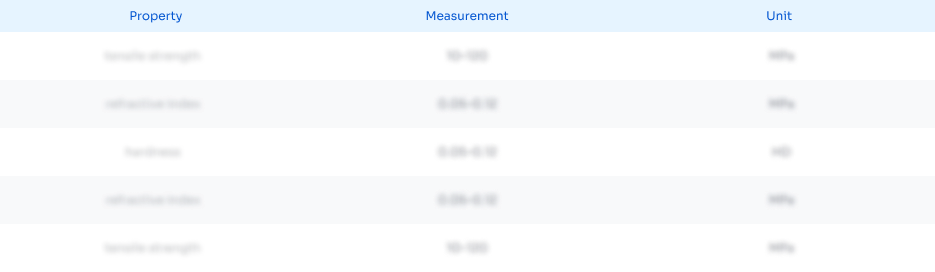
Abstract
Description
Claims
Application Information

- R&D
- Intellectual Property
- Life Sciences
- Materials
- Tech Scout
- Unparalleled Data Quality
- Higher Quality Content
- 60% Fewer Hallucinations
Browse by: Latest US Patents, China's latest patents, Technical Efficacy Thesaurus, Application Domain, Technology Topic, Popular Technical Reports.
© 2025 PatSnap. All rights reserved.Legal|Privacy policy|Modern Slavery Act Transparency Statement|Sitemap|About US| Contact US: help@patsnap.com