Airflow crushing tail gas afterheat utilization method for titanium white powder processing
A technology of airflow crushing and titanium dioxide, which is applied in the field of titanium dioxide processing, can solve the problems of low recycling rate and achieve the effects of sufficient absorption and purification, pollution reduction, and sufficient heat exchange
- Summary
- Abstract
- Description
- Claims
- Application Information
AI Technical Summary
Problems solved by technology
Method used
Image
Examples
Embodiment 1
[0039] combine figure 1 , a secondary waste heat recovery and utilization system of titanium dioxide post-processing airflow crushing tail gas in this embodiment is mainly composed of a heat exchanger 2, a liquid seal tank 4 and a hydraulic injector 1, and its air inlet is connected to the heat exchanger 2, Its water inlet end is connected with the circulating water pump 6, and its drain end is located in the liquid seal tank 4, and is connected with the turbulence heat exchange mechanism 8 at the drain end; the solution after heat exchange in the liquid seal tank 4 is used to supply water for the crude product.
[0040] The heat exchanger 2 is a commonly used heat exchange element at present. This device is mainly used for heat exchange for the first time. Since the heat carried by the original crushing air flow is relatively large, the heat exchange can be performed directly through the heat exchanger. When the heat exchange temperature reaches about 100°C, it is difficult t...
Embodiment 2
[0050] The secondary waste heat recovery and utilization system of titanium dioxide post-processing jet crushing exhaust gas in this embodiment has the same basic structure as that of embodiment 1, the difference is that in this embodiment, a water replenishment port is provided above the liquid seal tank 4, and The water flow is controlled by the replenishment control valve 7.
[0051] Preferably, a liquid level gauge can be set in the liquid seal tank 4. When the liquid level is lower than the set value, the water replenishment control valve 7 is automatically controlled to open to replenish water in the liquid seal tank; when the water level reaches a specified value, the water replenishment control valve is controlled. 7 Close, circulate the water in the liquid seal tank to absorb the heat in the exhaust gas.
[0052] The top of the liquid seal tank 4 is closed and is provided with an exhaust pipe 9. The exhaust gas after the energy is absorbed is concentrated and discharg...
Embodiment 3
[0054] A secondary waste heat recovery and utilization system for titanium dioxide post-treatment airflow crushing tail gas in this embodiment has the same basic structure as that of Embodiment 2, the difference is that the turbulence heat exchange mechanism 8 in this embodiment is mainly composed of external turbulence The chamber 82 and the inner turbulence chamber 83 are composed, and the outer turbulence chamber 82 communicates with the water outlet pipe 3 on the water jet 1 , so that the mixed medium flowing out of the water jet 1 enters the outer turbulence chamber 82 . The set inner turbulence chamber 83 communicates with the outer turbulence chamber 82, the top of the inner turbulence chamber 83 is open, and the bottom end of the inner turbulence chamber 83 is connected to the liquid seal tank 4 through a water pipe, then the water liquid in the outer turbulence chamber 82 can be It enters into the liquid seal tank 4 through the inner turbulence chamber 83, so as to rea...
PUM
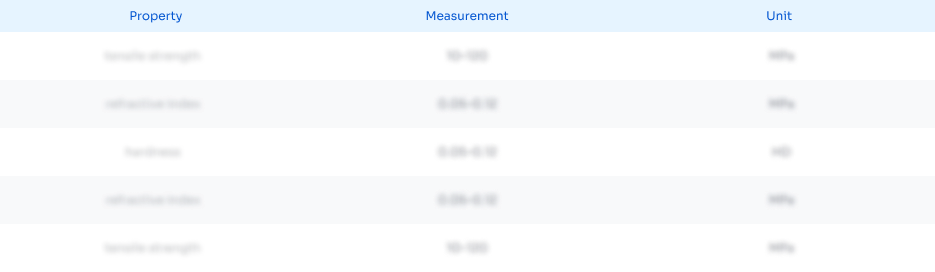
Abstract
Description
Claims
Application Information

- R&D Engineer
- R&D Manager
- IP Professional
- Industry Leading Data Capabilities
- Powerful AI technology
- Patent DNA Extraction
Browse by: Latest US Patents, China's latest patents, Technical Efficacy Thesaurus, Application Domain, Technology Topic, Popular Technical Reports.
© 2024 PatSnap. All rights reserved.Legal|Privacy policy|Modern Slavery Act Transparency Statement|Sitemap|About US| Contact US: help@patsnap.com