Frame joint assembly type wall assembly
A prefabricated and frame-based technology, which is applied to building components, walls, building structures, etc., can solve the problems of large amount of construction on site, long construction period, and slowdown of building construction speed, so as to speed up the construction progress, shorten the construction period, The effect of improving quality
- Summary
- Abstract
- Description
- Claims
- Application Information
AI Technical Summary
Problems solved by technology
Method used
Image
Examples
Embodiment approach
[0026] The first embodiment of the frame joint assembled wall member of the present invention includes a panel frame part 2 , a side column frame part 1 and a central column frame part 3 . The panel frame is composed of C-shaped steel 2-1 and connecting steel bars 2-2. The C-shaped steel has a through hole 2-1-1. The open end of the C-shaped steel has inward folded edges 2-1-2 and 2 -1-3. The side column frame is made of square steel pipe 1-1, and through holes are all arranged on the four side walls of square steel pipe 1-1. The central column frame is made of a square steel pipe 3-1, and through holes are also all arranged on the four side walls of the square steel pipe 3-1.
[0027] Fix the outer wall panels 4 on the outer sides of the panel frame and the central column frame, and fix the outer wall panels 4 on the two outer sides of the side column frames. The exterior wall panels are used as the EPS module insulation layer 4-1, the cement board protection layer 4-2 and ...
PUM
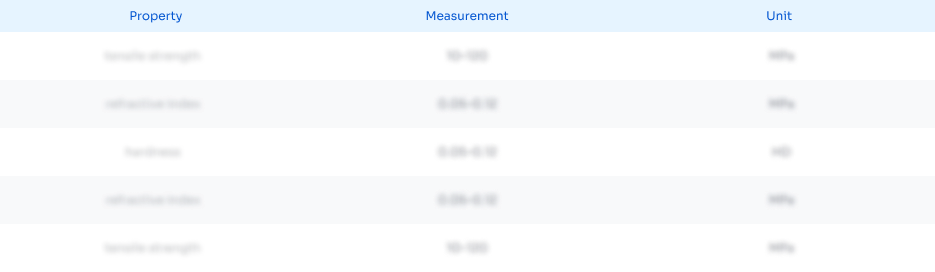
Abstract
Description
Claims
Application Information

- R&D
- Intellectual Property
- Life Sciences
- Materials
- Tech Scout
- Unparalleled Data Quality
- Higher Quality Content
- 60% Fewer Hallucinations
Browse by: Latest US Patents, China's latest patents, Technical Efficacy Thesaurus, Application Domain, Technology Topic, Popular Technical Reports.
© 2025 PatSnap. All rights reserved.Legal|Privacy policy|Modern Slavery Act Transparency Statement|Sitemap|About US| Contact US: help@patsnap.com