Multistage separation technology and device
A multi-stage separation and stage separation technology, which is applied in the fields of oil and gas and sewage treatment, can solve problems such as increased difficulty, poor separation effect of three-phase separators, and incompatible operating parameters, so as to reduce manufacturing and management operating costs, reduce Equipment safety management risk, achieve the effect of modularization
- Summary
- Abstract
- Description
- Claims
- Application Information
AI Technical Summary
Problems solved by technology
Method used
Image
Examples
Embodiment 1
[0027] In order to overcome the deficiencies of the prior art, the present embodiment provides a multi-stage separation process, which at least includes the following steps:
[0028] Step 1) Separation of the primary separation pipe: the incoming liquid enters the primary separation pipe 2 from the liquid inlet pipe 1, and after rapid dynamic separation, the associated gas enters the gas-liquid separator 3 for gas-liquid separation, and the separated gas passes through the gas outlet pipe For external transport, the liquid separated by the primary separation pipe 2 enters the upper pipe group 4 of the secondary separation pipe and the lower pipe group 5 of the secondary separation pipe;
[0029] Step 2) double separation of the secondary separation tube: the liquid entering the upper tube group 4 of the secondary separation tube and the lower tube group 5 of the secondary separation tube is separated at the same time, the upper tube group 4 of the secondary separation tube and ...
Embodiment 2
[0039] This embodiment provides a figure 1The multi-stage separation device shown includes a liquid inlet pipe 1, which is characterized in that: the liquid inlet pipe 1 is connected to the inlet of the first-stage separation pipe 2, and the upper outlet of the first-stage separation pipe 2 is connected to a gas-liquid separator 3 , the lower outlet of the primary separation tube 2 is connected to the inlet of the upper tube group 4 of the secondary separation tube and the inlet of the lower tube group 5 of the secondary separation tube, the upper tube group 4 of the secondary separation tube and the lower tube of the secondary separation tube Group 5 is connected in parallel, the upper outlets of the upper tube group 4 of the secondary separation tube and the lower tube group 5 of the secondary separation tube are connected to the oil outlet pipeline 6, the upper tube group 4 of the secondary separation tube and the lower tube group 5 of the secondary separation tube The lowe...
Embodiment 3
[0043] On the basis of embodiment 2, this embodiment provides a kind of figure 1 In the multi-stage separation device shown, the inlet end of the four-stage separation pipe 14 is also provided with an aeration head 22 , and the gas outlet of the gas-liquid separator 3 is connected to the aeration head 22 . The gas from the gas-liquid separator 3 enters the aeration head 22 in the four-stage separation pipe 14, and performs air flotation separation on the oil and water in the four-stage separation pipe 14 to further ensure the separation effect. With this structure, the aeration process Completed in a sealed room, it has the characteristics of good safety and easy management.
[0044] Further, in order to ensure the separation effect and safety, the first-stage separation pipe 2, the upper pipe group 4 of the second-stage separation pipe, the lower pipe group 5 of the second-stage separation pipe, the third-stage separation pipe 8 and the fourth-stage separation pipe 14 all inc...
PUM
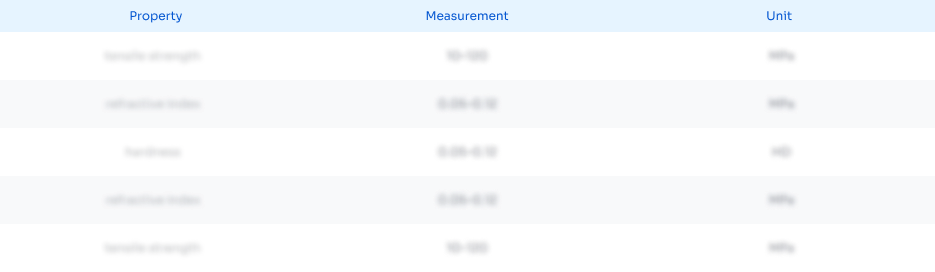
Abstract
Description
Claims
Application Information

- Generate Ideas
- Intellectual Property
- Life Sciences
- Materials
- Tech Scout
- Unparalleled Data Quality
- Higher Quality Content
- 60% Fewer Hallucinations
Browse by: Latest US Patents, China's latest patents, Technical Efficacy Thesaurus, Application Domain, Technology Topic, Popular Technical Reports.
© 2025 PatSnap. All rights reserved.Legal|Privacy policy|Modern Slavery Act Transparency Statement|Sitemap|About US| Contact US: help@patsnap.com