A microfiber composite molecular sieve membrane-loaded active component catalyst and its method and application
A technology of composite molecular sieve and active ingredient, which is applied in the catalytic oxidation of volatile organic compounds. In the field of microfiber composite molecular sieve membrane loaded active ingredient catalyst, it can solve the problems of low catalytic efficiency, poor dispersion, and insufficient loading of active components of catalysts. Uniformity and other issues to achieve the effect of improving catalytic activity, reducing energy consumption, and strengthening mass transfer and heat transfer of catalytic reactions
- Summary
- Abstract
- Description
- Claims
- Application Information
AI Technical Summary
Problems solved by technology
Method used
Image
Examples
Embodiment 1
[0048] (1) Preparation of paper-like microfiber composite molecular sieve membrane
[0049] (1-1) Add 3g of coniferous wood fiber and 6g of stainless steel fiber into an appropriate amount of water, and stir at high speed for 10 minutes in a fiber standard dissociator to form a uniform slurry, in which the diameter of the stainless steel fiber is 6.5μm; The sheet machine is used to copy the sheets, and after filtering water, a wet filter cake is formed to obtain a paper-type sintered stainless steel microfiber carrier precursor; the precursor is pressed and dried at 105°C for 12 hours; the dried paper-type sintered stainless steel microfiber carrier precursor N at a flow rate of 200mL / min 2 Sintering at 1050°C for 40 minutes under protection to obtain a paper-like sintered stainless steel microfiber carrier;
[0050] (1-2) The preparation method of MFI type molecular sieve membrane comprises the following steps: A) carrier pretreatment: the paper-like sintered stainless steel...
Embodiment 2
[0058] (1) Preparation of paper-like microfiber composite molecular sieve membrane
[0059] (1-1) Add 3g of coniferous wood fiber and 6g of stainless steel fiber into an appropriate amount of water, and stir at high speed for 10 minutes in a fiber standard dissociator to form a uniform slurry, in which the diameter of the stainless steel fiber is 6.5μm; The sheet machine was used to copy the sheets, and after filtering water, a wet filter cake was formed to obtain a paper-type sintered stainless steel microfiber carrier precursor; the precursor was pressed and dried at 105°C for 12 hours; the dried paper-type sintered stainless steel microfiber carrier precursor N at a flow rate of 200mL / min 2 Sintering at 1050°C for 40 minutes under protection to obtain a paper-like sintered stainless steel microfiber carrier;
[0060] (1-2) A) Carrier pretreatment: Cut the paper-like sintered stainless steel microfiber carrier into a suitable size, dissolve 3g of 3-aminopropyltrimethoxysila...
Embodiment 3
[0068] (1) The circular microfiber composite ZSM-5 molecular sieve membrane (the microfiber composite ZSM-5 molecular sieve membrane is the same as the microfiber composite ZSM-5 molecular sieve membrane prepared in Example 1) that has been cut into a diameter of 1 cm is dried at 110° C. 6h;
[0069] (2) Mix the microfiber composite ZSM-5 molecular sieve membrane of 2g drying with 0.39g iron acetylacetonate in the reaction bed, place the reaction bed in the middle of the quartz tube furnace, and carry out the reaction zone of the tube furnace Vacuum pumping-nitrogen operation, repeat three times, stop the ventilation after the tube furnace is filled with nitrogen to normal pressure; then carry out temperature programming reaction: increase the temperature from room temperature to 200 °C at a rate of 5 °C / min and keep it for 30 minutes, Then raise the temperature from 200°C to 250°C at 3°C / min and keep it for 30 minutes, and finally raise the temperature at 1°C / min to 280°C for...
PUM
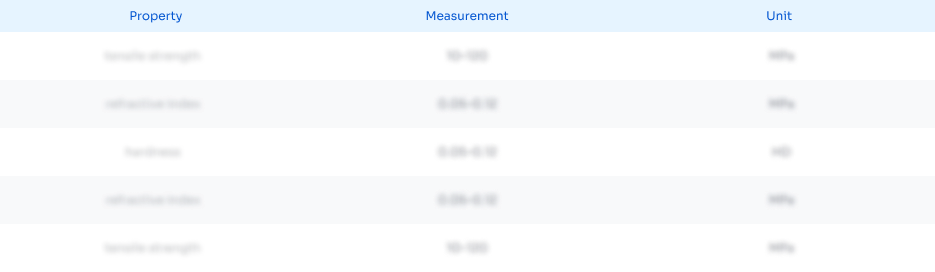
Abstract
Description
Claims
Application Information

- R&D
- Intellectual Property
- Life Sciences
- Materials
- Tech Scout
- Unparalleled Data Quality
- Higher Quality Content
- 60% Fewer Hallucinations
Browse by: Latest US Patents, China's latest patents, Technical Efficacy Thesaurus, Application Domain, Technology Topic, Popular Technical Reports.
© 2025 PatSnap. All rights reserved.Legal|Privacy policy|Modern Slavery Act Transparency Statement|Sitemap|About US| Contact US: help@patsnap.com