Ceramic surface polishing repairing process
A ceramic surface and process technology, applied in the field of ceramic surface polishing and repair technology, can solve the problems of surface glaze peeling, poor luminosity, affecting product performance, etc., and achieve the effect of improving adsorption force, high finish, anti-skid and other properties.
- Summary
- Abstract
- Description
- Claims
- Application Information
AI Technical Summary
Problems solved by technology
Method used
Examples
Embodiment Construction
[0017] A ceramic surface polishing and repairing process, the specific steps are as follows:
[0018] (1) Polishing: Use polishing liquid and grinding wheel to grind and polish the surface of the ceramic workpiece. After polishing, the polished surface is cleaned and dried;
[0019] (2) Pretreatment: Put the polished workpiece into the dopamine hydrochloride solution, take it out after shaking and soaking for 15 hours, wash it with deionized water twice, and send it to the metal salt solution with a temperature of 60°C, keep it warm for 30 minutes, and then let it stand. Set aside for 1 hour, then add organic ligands, continue shaking reaction at the same temperature for 10 hours, take out the workpiece, wash with deionized water for 3 times, then vacuum dry, and finally put the dried workpiece into an electric furnace, raise the temperature to 300°C, and keep it warm Discharge after 1h, and cool to room temperature naturally;
[0020] (3) Repair: Prepare the repair liquid, s...
PUM
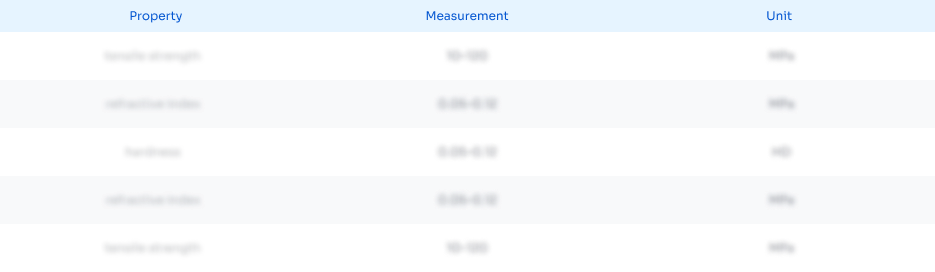
Abstract
Description
Claims
Application Information

- Generate Ideas
- Intellectual Property
- Life Sciences
- Materials
- Tech Scout
- Unparalleled Data Quality
- Higher Quality Content
- 60% Fewer Hallucinations
Browse by: Latest US Patents, China's latest patents, Technical Efficacy Thesaurus, Application Domain, Technology Topic, Popular Technical Reports.
© 2025 PatSnap. All rights reserved.Legal|Privacy policy|Modern Slavery Act Transparency Statement|Sitemap|About US| Contact US: help@patsnap.com