High-hardness self-protection overlaying flux-cored wire and preparation method thereof
A protection stack, high hardness technology, applied in welding equipment, welding media, manufacturing tools, etc., can solve the problems of difficult development of self-protected flux-cored welding wire, limited flux core space, etc., to avoid defects such as pores and improve hardness. , the effect of reducing manufacturing costs
- Summary
- Abstract
- Description
- Claims
- Application Information
AI Technical Summary
Problems solved by technology
Method used
Image
Examples
Embodiment 1
[0026] The drug core is prepared according to the following quality: 80g of high-carbon ferrochrome, 9.5g of silicon-manganese alloy, 1g of aluminum-magnesium alloy, 2g of graphite, 0.5g of boron nitride, 5g of rutile and 2g of fluorite. All the powders taken passed through an 80-mesh sieve. Put the various powders taken into the powder mixer, mix for 40 minutes, then add the mixed powder into the U-shaped 16×0.3mm H08A carbon steel belt groove, and the filling rate is 55%. Then close the U-shaped groove so that the powder is wrapped therein. Then make it pass through one or more of the wire drawing dies with diameters of 4.10mm, 3.80mm, 3.45mm, 3.15mm, 2.85mm, 2.60mm, and 2.40mm, draw and reduce the diameter one by one, and finally obtain a diameter of 2.40~4.10mm welding wire products. The welding current is 280-400A, the welding voltage is 28-36V, and the welding speed is 2.4m / min. The hardness and wear resistance of surfacing metal are shown in Table 1.
Embodiment 2
[0028] The drug core is prepared according to the following quality: 76g of high-carbon ferrochromium, 8g of silicon-manganese alloy, 2g of aluminum-magnesium alloy, 0.8g of graphite, 1.2g of boron nitride, 6g of rutile and 6g of fluorite. All the powders taken passed through an 80-mesh sieve. Put the various powders taken into the powder mixer, mix for 40 minutes, then add the mixed powder into the U-shaped 16×0.3mm H08A carbon steel belt groove, and the filling rate is 50%. Then close the U-shaped groove so that the powder is wrapped therein. Then make it pass through one or more of the wire drawing dies with diameters of 4.10mm, 3.80mm, 3.45mm, 3.15mm, 2.85mm, 2.60mm, and 2.40mm, draw and reduce the diameter one by one, and finally obtain a diameter of 2.40~4.10mm welding wire products. The welding current is 280-400A, the welding voltage is 28-36V, and the welding speed is 2.4m / min. The hardness and wear resistance of surfacing metal are shown in Table 1.
Embodiment 3
[0030] The drug core is prepared according to the following quality: 70g of high-carbon ferrochrome, 10g of silicon-manganese alloy, 1g of aluminum-magnesium alloy, 3.6g of graphite, 1.2g of boron nitride, 10g of rutile and 4.2g of fluorite. All the powders taken passed through an 80-mesh sieve. Put the various powders taken into the powder mixer, mix for 40 minutes, then add the mixed powder into the U-shaped 16×0.3mm H08A carbon steel belt groove, and the filling rate is 45%. Then close the U-shaped groove so that the powder is wrapped therein. Then make it pass through one or more of the wire drawing dies with diameters of 4.10mm, 3.80mm, 3.45mm, 3.15mm, 2.85mm, 2.60mm, and 2.40mm, draw and reduce the diameter one by one, and finally obtain a diameter of 2.40~4.10mm welding wire products. The welding current is 280-400A, the welding voltage is 28-36V, and the welding speed is 2.4m / min. The hardness and wear resistance of surfacing metal are shown in Table 1.
PUM
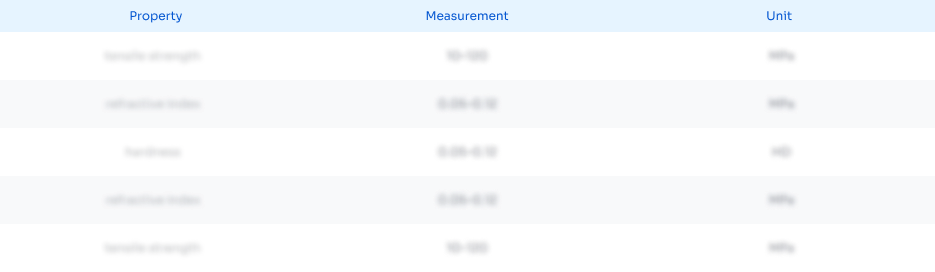
Abstract
Description
Claims
Application Information

- Generate Ideas
- Intellectual Property
- Life Sciences
- Materials
- Tech Scout
- Unparalleled Data Quality
- Higher Quality Content
- 60% Fewer Hallucinations
Browse by: Latest US Patents, China's latest patents, Technical Efficacy Thesaurus, Application Domain, Technology Topic, Popular Technical Reports.
© 2025 PatSnap. All rights reserved.Legal|Privacy policy|Modern Slavery Act Transparency Statement|Sitemap|About US| Contact US: help@patsnap.com