Technique for producing large and medium-sized cylindrical iron castings through clay green sand molding
A technology of green sand and iron castings, which is applied in the field of sand casting, can solve the problems of not being suitable for the production and processing of general iron castings, the influence of casting product quality, and high production costs, so as to achieve environmental and social benefits, shorten the production process, and use The effect of performance improvement
- Summary
- Abstract
- Description
- Claims
- Application Information
AI Technical Summary
Problems solved by technology
Method used
Image
Examples
Embodiment Construction
[0010] The process of producing large and medium-sized cylindrical iron castings by clay green sand molding is realized according to the following process steps: sand preparation—molding—core making—box assembly—pouring—shaking out—cleaning—inspection and repair; the core making steps are as follows: 1. Design the corresponding sand core structure according to the structure of the processed cylindrical iron casting. The sand core is designed with a through hole structure or blind hole structure in the axial direction to form a cavity structure; 2. Draw the inner mold according to the structure of the sand core , the blueprint of the outer mold; 3, adopt steel plate to make inner mold 5, outer mold according to drawing, wherein evenly opened with some exhaust through-holes 6 on the inner mold 5; 4, make cavity sand core: combine outer mold and inner mold 5 It is fixed on a flat floor, and clay green sand is filled between the outer mold and the inner mold 5, and the outer mold i...
PUM
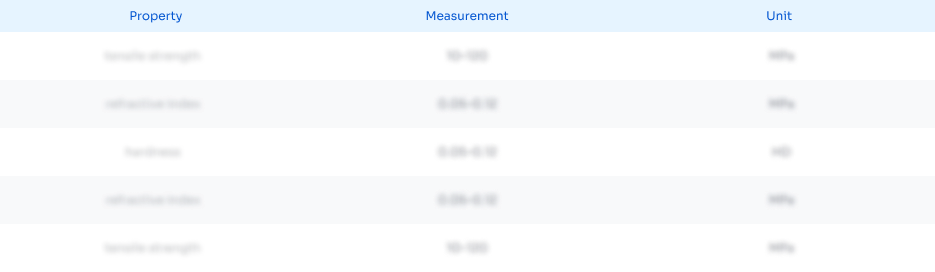
Abstract
Description
Claims
Application Information

- R&D
- Intellectual Property
- Life Sciences
- Materials
- Tech Scout
- Unparalleled Data Quality
- Higher Quality Content
- 60% Fewer Hallucinations
Browse by: Latest US Patents, China's latest patents, Technical Efficacy Thesaurus, Application Domain, Technology Topic, Popular Technical Reports.
© 2025 PatSnap. All rights reserved.Legal|Privacy policy|Modern Slavery Act Transparency Statement|Sitemap|About US| Contact US: help@patsnap.com