Spiral groove forming die
A technology of spiral groove and forming die, which is applied in the field of metal stamping processing, can solve the problems of inability to integrate into stamping processing, high investment cost of manipulators, and low profit margin, etc., to achieve the effects of ensuring coaxiality, avoiding shape distortion, and improving processing efficiency
- Summary
- Abstract
- Description
- Claims
- Application Information
AI Technical Summary
Problems solved by technology
Method used
Image
Examples
Embodiment Construction
[0041] The present invention will be described in further detail below in conjunction with specific embodiments.
[0042] Such as Figure 1 to Figure 4 As shown, a spiral groove molding die of the present invention includes an upper template 11 and a lower template 21 arranged oppositely, and the upper template 11 is provided with a forming punch 12 located in the middle; the lower template 21 is provided with a corresponding forming punch 12 The molding block 22 and several forming sliders 23 that can move radially along the forming block 22 around the forming block 22, the forming punch 12 and the forming block 22 can be combined to form a thread forming groove (not marked) , The forming slider 23 has a forming ridge 231 that can be pressed into the thread forming groove. During processing, the fuel tank filling port 3 material without a spiral groove is set on the forming bracket 22, and in the mold closing process, the forming punch 12 is spliced with the forming bracke...
PUM
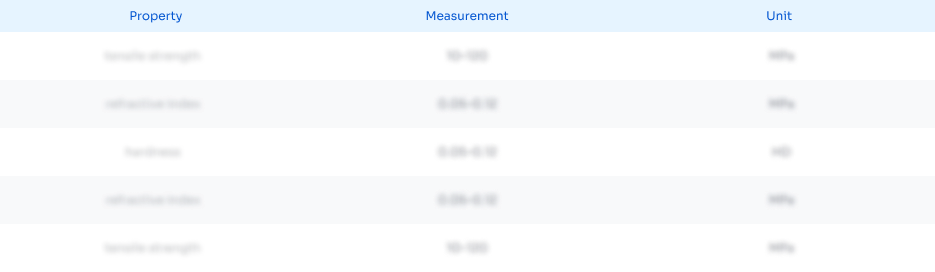
Abstract
Description
Claims
Application Information

- Generate Ideas
- Intellectual Property
- Life Sciences
- Materials
- Tech Scout
- Unparalleled Data Quality
- Higher Quality Content
- 60% Fewer Hallucinations
Browse by: Latest US Patents, China's latest patents, Technical Efficacy Thesaurus, Application Domain, Technology Topic, Popular Technical Reports.
© 2025 PatSnap. All rights reserved.Legal|Privacy policy|Modern Slavery Act Transparency Statement|Sitemap|About US| Contact US: help@patsnap.com