Method and apparatus for producing synthetic staple fibers
A technology for synthesizing staple fibers and equipment, which is applied in the field of manufacturing synthetic staple fibers/cut fibers, and can solve problems such as the inability to achieve constant guide tow and so on.
- Summary
- Abstract
- Description
- Claims
- Application Information
AI Technical Summary
Problems solved by technology
Method used
Image
Examples
Embodiment Construction
[0035] exist Figures 1 to 4 An embodiment of a device according to the invention is shown in several views. figure 1 shows a side view of the melt-spinning apparatus, figure 2 shows a side view of the fiber processing device arranged behind, Figure 3.1 schematically shows a top view of the laying station, Figure 3.2 schematically shows a front view of the laying station, Figure 4 A top view of the can creel is shown schematically. The following description applies to all drawings unless it is explicitly indicated which drawing(s) are referred to.
[0036] exist figure 1An embodiment of a melt-spinning device used in the method according to the invention, for example in an apparatus according to the invention, is shown in , in order to form a plurality of fiber slivers newly extruded from a tow. The melt spinning device 1 has a spinning beam 5, on the bottom side of which a plurality of spinning nozzle units 6.1, 6.2 and 6.3 are arranged. The number of spinning nozz...
PUM
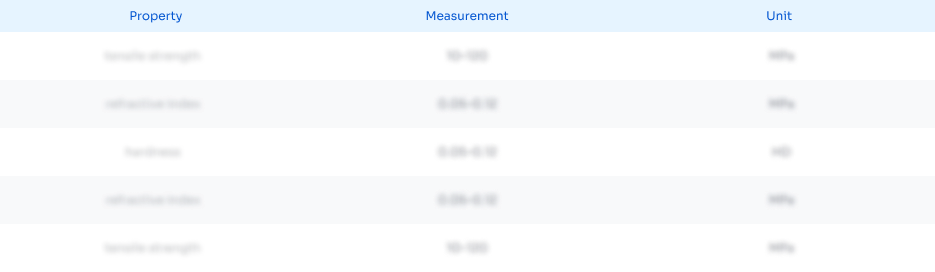
Abstract
Description
Claims
Application Information

- R&D
- Intellectual Property
- Life Sciences
- Materials
- Tech Scout
- Unparalleled Data Quality
- Higher Quality Content
- 60% Fewer Hallucinations
Browse by: Latest US Patents, China's latest patents, Technical Efficacy Thesaurus, Application Domain, Technology Topic, Popular Technical Reports.
© 2025 PatSnap. All rights reserved.Legal|Privacy policy|Modern Slavery Act Transparency Statement|Sitemap|About US| Contact US: help@patsnap.com