Water-based velvet effect auxiliary agent applicable to synthetic leather
A synthetic leather and water-based technology, applied in the direction of textiles and papermaking, can solve the problems of affecting the processing environment, increasing the cost of wastewater treatment, and the difficulty of wastewater treatment, etc., and achieves a long-lasting velvet feel, strong environmental protection in processing, and soft hand feeling. Effect
- Summary
- Abstract
- Description
- Claims
- Application Information
AI Technical Summary
Problems solved by technology
Method used
Image
Examples
Embodiment 1
[0028] (1) Add 15g of down fiber / polyvinylpyrrolidone and 0.5g of polyethylene oxide to 100g of water, and heat up to reflux state and mix for 15 minutes, then add 2g of polyvinyl alcohol modified activated clay and 0.15g of nano-titanium dioxide, and continue to reflux for heat preservation Mixed for 15min, then naturally cooled to room temperature to obtain material I;
[0029] (2) Add 5g soybean protein fiber / poloxamer and 0.5g polyethylene glycol 4000 to 50g water, and heat up to reflux state and mix for 15min, then add 0.3g polyaluminum sulfate ferric chloride and 0.05g pyrophosphorous acid tin, continue to reflux insulation and mix for 5min, then naturally cool to room temperature to obtain material II;
[0030] (3) Add material II, 3g of microcrystalline cellulose / chitosan, 2g of cationic polyacrylamide and 1g of sodium carboxymethylcellulose to material I, mix well and send it into a ball mill, pass through a 300-mesh sieve after ball milling for 8 hours , the resulti...
Embodiment 2
[0035] (1) Add 20g of down fiber / polyvinylpyrrolidone and 0.5g of polyethylene oxide to 100g of water, and heat up to reflux state and mix for 15 minutes, then add 3g of polyvinyl alcohol modified activated clay and 0.3g of nano-titanium dioxide, and continue to reflux for heat preservation Mixed for 15min, then naturally cooled to room temperature to obtain material I;
[0036] (2) Add 10 g of soybean protein fiber / poloxamer and 0.5 g of polyethylene glycol 4000 to 50 g of water, heat up to reflux and mix for 15 minutes, then add 0.5 g of polyaluminum sulfate ferric chloride and 0.05 g of pyrophosphorous acid tin, continue to reflux insulation and mix for 5min, then naturally cool to room temperature to obtain material II;
[0037](3) Add material II, 5g microcrystalline cellulose / chitosan, 2g cationic polyacrylamide and 2g sodium carboxymethyl cellulose to material I, mix well and send it into a ball mill, pass through a 300-mesh sieve after ball milling for 8 hours , the r...
Embodiment 3
[0057] Add the cashmere feeling auxiliary agent of equivalent embodiment 1, embodiment 2, comparative example 1, comparative example 2 and comparative example 3 respectively in the water-based polyurethane slurry (concrete raw material ratio is as shown in table 1, wherein cashmere feeling auxiliary agent Adding agent is 1.5wt%, in terms of solid content), and through the same processing technology, synthetic leather is made, and the cashmere-related properties of the synthetic leather are tested, and the test results are shown in Table 2.
[0058] Table 1 Synthetic leather preparation slurry ratio table
[0059]
[0060]
[0061] The synthetic leather performance test result of table 2
[0062]
PUM
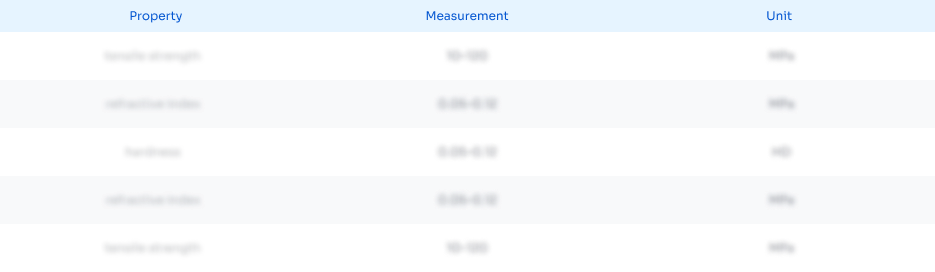
Abstract
Description
Claims
Application Information

- R&D
- Intellectual Property
- Life Sciences
- Materials
- Tech Scout
- Unparalleled Data Quality
- Higher Quality Content
- 60% Fewer Hallucinations
Browse by: Latest US Patents, China's latest patents, Technical Efficacy Thesaurus, Application Domain, Technology Topic, Popular Technical Reports.
© 2025 PatSnap. All rights reserved.Legal|Privacy policy|Modern Slavery Act Transparency Statement|Sitemap|About US| Contact US: help@patsnap.com