Production increasing technology of dimethyl carbonate
A technology of dimethyl carbonate and process is applied in the field of increasing production of dimethyl carbonate, and can solve the problems of unclear reaction mechanism, unstable DMC output, complex reaction by-products and the like
- Summary
- Abstract
- Description
- Claims
- Application Information
AI Technical Summary
Problems solved by technology
Method used
Image
Examples
Embodiment 1
[0027] Take 180g of dimethyl carbonate in a 250ml four-neck flask, stir with a magnetic force, and the intensity of ultraviolet light is 1325uW / cm 2 The rate of chlorine flow is 135ml / min, and the reaction is carried out, and the tail gas is absorbed by a two-stage method. The process is condensed and refluxed to reduce the loss of raw materials under conditions such as volatilization at high temperature and being carried out by gas. React at 35-45°C for 14 hours, blow off with inert gas for half an hour, wait for the reaction product to cool to room temperature, use a pipette gun and an analytical balance to calculate the specific gravity of the chlorinated solution to be 1.1001. Then react at 75-85°C for 14 hours, stop the light, blow off with an inert gas for half an hour, and cool the reaction product to room temperature to obtain a chlorinated solution with a specific gravity of 1.555. The weight gain of the system was 176.1984g, and the chlorination rate of the trichlor...
Embodiment 2
[0031] Take 180g of dimethyl carbonate in a 250ml four-necked flask, stir it under magnetic force, and the intensity of ultraviolet light is 1000uW / cm 2 The rate of chlorine flow is 135ml / min, and the reaction is carried out, and the tail gas is absorbed by a two-stage method. The process is condensed and refluxed to reduce the loss of raw materials under conditions such as volatilization at high temperature and being carried out by gas. React at 35-45°C for 12 hours, blow off with inert gas for half an hour, wait for the reaction product to cool to room temperature, use a pipette gun and an analytical balance to calculate the specific gravity of the chlorinated solution to be 1.0001. Then react at 75-85°C for 12 hours, stop the light, blow off with an inert gas for half an hour, and cool the reaction product to room temperature to obtain a chlorinated solution with a specific gravity of 1.446. The weight gain of the system was 136.6407g, and the chlorination rate of trichlor...
Embodiment 3
[0034] Take 180g of dimethyl carbonate in a 250ml four-necked flask, and react under magnetic stirring, the ultraviolet light intensity is 1325uW / cm2 and the rate of chlorine flow is 135ml / min, and the tail gas is absorbed by a two-stage method. The process is condensed and refluxed to reduce the loss of raw materials under conditions such as volatilization at high temperature and being carried out by gas. The reaction was carried out at 35-45°C for 12 hours, blown off with an inert gas for half an hour, and the reaction product was cooled to room temperature, and the specific gravity of the chlorinated solution was calculated to be 1.0868 with a pipette gun and an analytical balance. Then react at 75-85°C for 12 hours, stop the light, blow off with an inert gas for half an hour, and cool the reaction product to room temperature to obtain a chlorinated solution with a specific gravity of 1.527. The weight gain of the system was 163.1431g, and the chlorination rate of the trich...
PUM
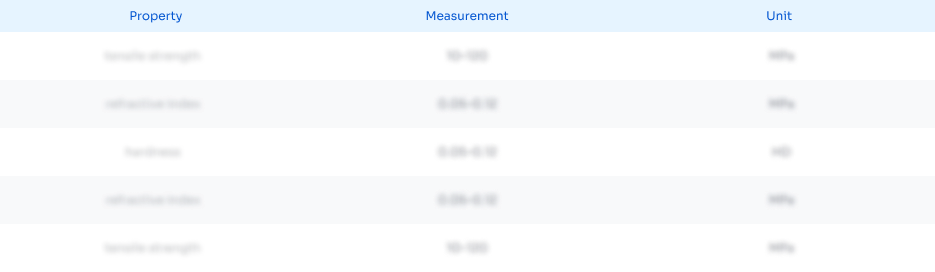
Abstract
Description
Claims
Application Information

- R&D
- Intellectual Property
- Life Sciences
- Materials
- Tech Scout
- Unparalleled Data Quality
- Higher Quality Content
- 60% Fewer Hallucinations
Browse by: Latest US Patents, China's latest patents, Technical Efficacy Thesaurus, Application Domain, Technology Topic, Popular Technical Reports.
© 2025 PatSnap. All rights reserved.Legal|Privacy policy|Modern Slavery Act Transparency Statement|Sitemap|About US| Contact US: help@patsnap.com