Carburization preventing coating for ultralow carbon casting resin sand casting
A technology of anti-carburizing paint and resin sand, which is used in casting and molding equipment, coatings, molds, etc., can solve the problems of poor surface stability of sand molds, large grinding allowance, and metal waste.
- Summary
- Abstract
- Description
- Claims
- Application Information
AI Technical Summary
Problems solved by technology
Method used
Examples
Embodiment 1
[0025] (1) Add 3kg carboxymethyl chitosan oligosaccharide and 2kg molecular sieve raw powder to 10kg activated clay, heat up to 115-120°C and keep grinding for 15min, then add 2kg asbestos powder and 0.05kg yttrium oxide, continue to heat at 115-120°C Heat preservation and grinding for 15 minutes to obtain modified clay powder;
[0026] (2) Add 1 kg of hydrolyzed polymaleic anhydride and 1 kg of nano-titanium dioxide to 5 kg of fly ash, and raise the temperature to 110-115 ° C for 30 minutes of heat preservation and grinding to obtain modified fly ash;
[0027] (3) Add 25kg of resin-modified pozzolan, modified clay powder and 5kg of resin-modified ceramic micropowder to 200kg of water, mix well, seal and stand for 1 hour in an environment of 0-5°C, then add modified fly ash and 2kg Sepiolite fiber powder, heated to reflux state and mixed for 15 minutes, the resulting mixture was naturally cooled to room temperature and then sent to a ball mill, ball milled until the output par...
Embodiment 2
[0031] (1) Add 5kg carboxymethyl chitosan oligosaccharide and 2kg molecular sieve raw powder to 15kg activated clay, heat up to 115-120°C and keep grinding for 15min, then add 3kg asbestos powder and 0.05kg yttrium oxide, continue to heat at 115-120°C Heat preservation and grinding for 15 minutes to obtain modified clay powder;
[0032] (2) Add 1 kg of hydrolyzed polymaleic anhydride and 1 kg of nano-titanium dioxide to 10 kg of fly ash, and raise the temperature to 110-115 ° C for 30 minutes of heat preservation and grinding to obtain modified fly ash;
[0033] (3) Add 30kg of resin-modified pozzolan, modified clay powder and 3kg of resin-modified ceramic micropowder to 200kg of water, mix well, seal and stand for 1 hour in an environment of 0-5°C, then add modified fly ash and 2kg Sepiolite fiber powder, heated to reflux state and mixed for 15 minutes, the resulting mixture was naturally cooled to room temperature and then sent to a ball mill, ball milled until the output pa...
Embodiment 3
[0054] The anti-carburization coatings made in Example 1, Example 2, Comparative Example 1, Comparative Example 2, Comparative Example 3 and Comparative Example 4 were sprayed on the surface of the same batch of sand molds made through the same molding sand, and used after the coating was completely dry. The casting of the upper crown and the lower ring of the stainless steel runner of the hydropower station, and the thickness of the surface carburized layer of the castings produced by the processing are measured. The results are shown in Table 1.
[0055] Table 1 Surface carburized layer thickness of castings produced by machining
[0056] Test items Example 1 Example 2 Comparative example 1 Comparative example 2 Comparative example 3 Comparative example 4 Carburized layer thickness 2.32mm 2.28mm 2.56mm 2.83mm 3.24mm 3.85mm
PUM
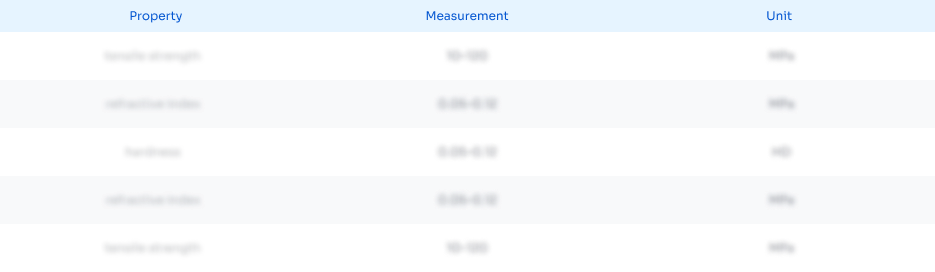
Abstract
Description
Claims
Application Information

- R&D
- Intellectual Property
- Life Sciences
- Materials
- Tech Scout
- Unparalleled Data Quality
- Higher Quality Content
- 60% Fewer Hallucinations
Browse by: Latest US Patents, China's latest patents, Technical Efficacy Thesaurus, Application Domain, Technology Topic, Popular Technical Reports.
© 2025 PatSnap. All rights reserved.Legal|Privacy policy|Modern Slavery Act Transparency Statement|Sitemap|About US| Contact US: help@patsnap.com