Preparation method for amorphous alloy/pure copper layered composite material
A technology of layered composite materials and amorphous alloys, applied in the field of materials, can solve problems affecting the overall mechanical properties of composite materials, crystallization of amorphous alloys at the interface, and complex processes
- Summary
- Abstract
- Description
- Claims
- Application Information
AI Technical Summary
Problems solved by technology
Method used
Image
Examples
Embodiment 1
[0018] The preparation method of amorphous alloy / pure copper layered composite material, its step comprises:
[0019] Step 1: Zr 41.2 Ti 13.8 Ni 10 Cu 12.5 be 22.5 Amorphous alloy adopts high-vacuum non-consumable arc melting furnace to melt master alloy, spray cast into Zirconium-based bulk amorphous alloy rods; Zr-based bulk amorphous alloy rods and copper The sample was smoothed with 1200# sandpaper, and the upper and lower surfaces of the amorphous sample and the copper sample were guaranteed to be parallel to each other; then it was placed in acetone and alcohol for 5 minutes of ultrasonic vibration cleaning, in order to reduce the influence of oxygen atoms on the interface, after drying Immediately put into the vacuum autoclave;
[0020] Step 2: Pump high vacuum to 10 -5 Pa, and then heated to the hot pressing temperature of 370°C at a heating rate of 40k / min, with a deformation rate of 10 -3 the s -1 down, will Zirconium-based bulk amorphous alloy rods ...
Embodiment 2
[0022] The preparation method of amorphous alloy / pure copper layered composite material, its step comprises:
[0023] Step 1: Zr 41.2 Ti 13.8 Ni 10 Cu 12.5 be 22.5 Amorphous alloy adopts high-vacuum non-consumable arc melting furnace to melt master alloy, spray cast into Zirconium-based bulk amorphous alloy rods; Zr-based bulk amorphous alloy rods and copper The sample was smoothed with 1200# sandpaper, and the upper and lower surfaces of the amorphous sample and the copper sample were guaranteed to be parallel to each other; then it was placed in acetone and alcohol for 5 minutes of ultrasonic vibration cleaning, in order to reduce the influence of oxygen atoms on the interface, after drying Immediately put into the vacuum autoclave;
[0024] Step 2: Pump high vacuum to 10 -4 Pa, and then heated to the hot pressing temperature of 390°C at a heating rate of 40k / min, with a deformation rate of 10-3s-1, the Zirconium-based bulk amorphous alloy rods were diffusion-...
Embodiment 3
[0026] The preparation method of amorphous alloy / pure copper layered composite material, its step comprises:
[0027] Step 1: Zr 41.2 Ti 13.8 Ni 10 Cu 12.5 be 22.5 Amorphous alloy adopts high-vacuum non-consumable arc melting furnace to melt master alloy, spray cast into Zirconium-based bulk amorphous alloy rods; Zr-based bulk amorphous alloy rods and copper The sample was smoothed with 1200# sandpaper, and the upper and lower surfaces of the amorphous sample and the copper sample were guaranteed to be parallel to each other; then it was placed in acetone and alcohol for 5 minutes of ultrasonic vibration cleaning, in order to reduce the influence of oxygen atoms on the interface, after drying Immediately put into the vacuum autoclave;
[0028] Step 2: Pump high vacuum to 10 -3 Pa, and then heated to the hot pressing temperature of 400°C at a heating rate of 40k / min, with a deformation rate of 10 -3 the s -1 down, will Zirconium-based bulk amorphous alloy rods ...
PUM
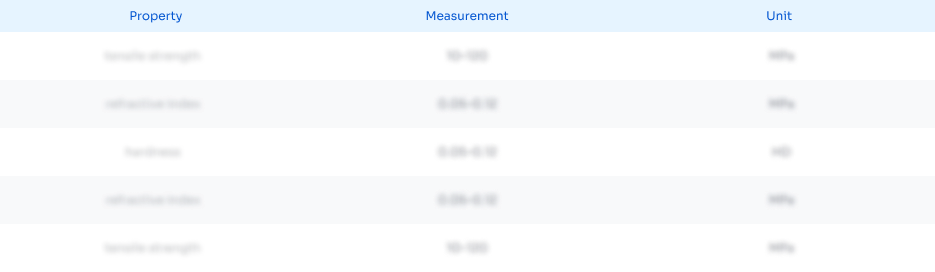
Abstract
Description
Claims
Application Information

- R&D
- Intellectual Property
- Life Sciences
- Materials
- Tech Scout
- Unparalleled Data Quality
- Higher Quality Content
- 60% Fewer Hallucinations
Browse by: Latest US Patents, China's latest patents, Technical Efficacy Thesaurus, Application Domain, Technology Topic, Popular Technical Reports.
© 2025 PatSnap. All rights reserved.Legal|Privacy policy|Modern Slavery Act Transparency Statement|Sitemap|About US| Contact US: help@patsnap.com