Porous silicon negative electrode material covered by composite carbon and preparing method thereof
A negative electrode material, porous silicon technology, applied in the direction of battery electrodes, structural parts, electrical components, etc., can solve the problems affecting the coulombic efficiency of the battery, the looseness of the graphene coating layer, the impact of silicon cycle, etc., to achieve coulombic efficiency and avoid direct Contact, the effect of ensuring the effective capacity
- Summary
- Abstract
- Description
- Claims
- Application Information
AI Technical Summary
Problems solved by technology
Method used
Image
Examples
Embodiment 1
[0057] (1) Preparation of alloy microspheres
[0058] First, prepare an aluminum-silicon alloy with a mass fraction of silicon of 10%, and melt magnesium and silicon in proportion. The melting temperature is 800°C. After the alloy ingot is obtained, it is sprayed. The atomization temperature is 1000°C. By controlling the air flow and the material Ratio, to obtain Al-Si alloy spheres with a median diameter of 20um.
[0059] (2) De-alloying of micro-alloy balls and the first layer of carbon coating
[0060] Put the alloy ball obtained in step (1) into the graphene oxide aqueous solution with a concentration of 1mg / mL, the magnesium in the alloy will fully reduce the graphene oxide, and after reacting for 1h, add the obtained coated sample to the concentration In 1mol / L hydrochloric acid, corrode to obtain graphene-coated porous silicon.
[0061] (3) The second layer of carbon coating
[0062] The graphene-coated porous silicon obtained in step (2) is added to the tetrahydrofu...
Embodiment 2
[0064] (1) Preparation of alloy microspheres
[0065] Firstly, a magnesium-silicon alloy with a silicon mass fraction of 10% is prepared, and the magnesium and silicon are smelted in proportion. The melting temperature is 700°C. After the alloy ingot is obtained, it is sprayed. The atomization temperature is 700°C. By controlling the air flow and the material Ratio, to obtain a magnesium-silicon alloy ball with a median diameter of 10um.
[0066] (2) De-alloying of micro-alloy balls and the first layer of carbon coating
[0067] Put the alloy ball obtained in step (1) into the graphite oxide aqueous solution with a concentration of 0.5mg / mL, the magnesium in the alloy will fully reduce the graphene oxide, and after reacting for 1h, add the obtained coated sample to the concentration In 0.2mol / L hydrochloric acid, corrode to obtain graphene-coated porous silicon.
[0068] (3) The second layer of carbon coating
[0069] The graphene-coated porous silicon obtained in step (2) ...
Embodiment 3
[0071] (1) Preparation of alloy microspheres
[0072] First, an aluminum-silicon alloy with a silicon mass fraction of 10% is prepared, and the melting temperature is 750°C. After the alloy ingot is obtained, it is sprayed, and the ratio of the air flow to the material is adjusted to obtain an aluminum-silicon alloy ball with a median diameter of 10um.
[0073] (2) De-alloying of micro-alloy balls and the first layer of carbon coating
[0074] Add the alloy balls obtained in step (1) into hydrochloric acid with a concentration of 1 mol / L, and fully corrode to obtain porous silicon. The obtained porous silicon is put into a citric acid alcohol solution with a mass fraction of 10%, and after being fully stirred, the above-mentioned sample is dried by spray drying, and the obtained sample is put into a carbonization furnace, nitrogen is used as a protective atmosphere, 700 ℃ carbonization for 5h.
[0075] (3) The second layer of carbon coating
[0076] The carbon-coated porous...
PUM
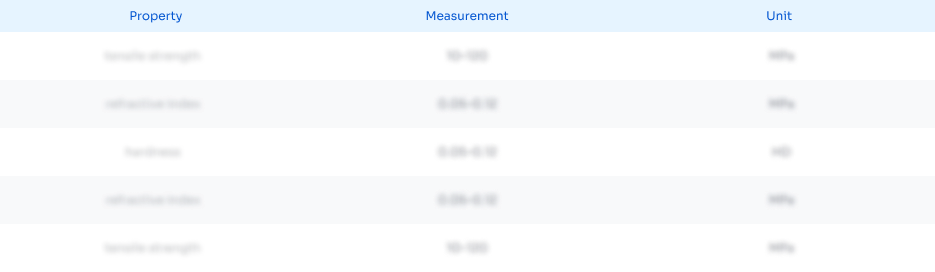
Abstract
Description
Claims
Application Information

- R&D
- Intellectual Property
- Life Sciences
- Materials
- Tech Scout
- Unparalleled Data Quality
- Higher Quality Content
- 60% Fewer Hallucinations
Browse by: Latest US Patents, China's latest patents, Technical Efficacy Thesaurus, Application Domain, Technology Topic, Popular Technical Reports.
© 2025 PatSnap. All rights reserved.Legal|Privacy policy|Modern Slavery Act Transparency Statement|Sitemap|About US| Contact US: help@patsnap.com