Microencapsulated expandable graphite, preparation method thereof, and application of microencapsulated expandable graphite in preparing composite rigid polyurethane foam
A composite polyurethane and expanded graphite technology, applied in chemical instruments and methods, dyed low-molecular-weight organic compound treatment, dyed high-molecular-weight organic compound treatment, etc., to achieve high flame retardant efficiency, high mechanical properties and flame retardant properties, and low addition amount Effect
- Summary
- Abstract
- Description
- Claims
- Application Information
AI Technical Summary
Problems solved by technology
Method used
Image
Examples
Embodiment 1
[0039] Preparation of microencapsulated expandable graphite:
[0040] (1) Preparation of melamine resin prepolymer: Mix and stir melamine and formaldehyde solution at a certain mass ratio, then add triethanolamine aqueous solution to adjust the pH to 7.0, slowly heat up to 60°C and react for 2 hours to obtain viscous transparent water-soluble melamine Resin prepolymer; wherein the mass fraction of formaldehyde solution is 37%, the mass fraction of triethanolamine aqueous solution is 10%, and the mass ratio of melamine and formaldehyde solution is 1:2;
[0041] (2) Expandable graphite coated with melamine resin prepolymer: add expandable graphite to absolute ethanol, stir ultrasonically for 0.5h, add cationic surfactant cetyltrimethylammonium chloride, stir for 1h, and finally Slowly add melamine resin prepolymer, adjust the pH to 3.5 with dilute hydrochloric acid, slowly raise the temperature to 65°C, filter after 2 hours of reaction, and vacuum dry to obtain expandable graphi...
Embodiment 2
[0057] Preparation of microencapsulated expandable graphite:
[0058] (1) Preparation of melamine resin prepolymer: Mix and stir melamine and formaldehyde solution at a certain mass ratio, then add triethanolamine aqueous solution to adjust the pH to 8.0, slowly heat up to 85°C and react for 5 hours to obtain viscous transparent water-soluble melamine Resin prepolymer; wherein the mass fraction of formaldehyde solution is 37%, the mass fraction of triethanolamine aqueous solution is 10%, and the mass ratio of melamine and formaldehyde solution is 1:5;
[0059] (2) Expandable graphite coated with melamine resin prepolymer: Add expandable graphite to absolute ethanol, stir ultrasonically for 1 hour, add cationic surfactant cetyltrimethylammonium chloride, stir for 2 hours, and finally slowly Add melamine resin prepolymer, adjust the pH to 5.5 with dilute hydrochloric acid, slowly heat up to 85°C, filter after reacting for 5 hours, and vacuum-dry to obtain expandable graphite mic...
Embodiment 3
[0080] Preparation of microencapsulated expandable graphite:
[0081] (1) Preparation of melamine resin prepolymer: Mix and stir melamine and formaldehyde solution at a certain mass ratio, then add triethanolamine aqueous solution to adjust the pH to 7.5, slowly heat up to 80°C for 4 hours, and obtain viscous transparent water-soluble melamine Resin prepolymer; wherein the mass fraction of formaldehyde solution is 37%, the mass fraction of triethanolamine aqueous solution is 10%, and the mass ratio of melamine and formaldehyde solution is 1:3;
[0082] (2) Expandable graphite coated with melamine resin prepolymer: Add expandable graphite to absolute ethanol, stir ultrasonically for 40min, add cationic surfactant cetyltrimethylammonium chloride, stir for 1.5h, and finally Slowly add the melamine resin prepolymer, adjust the pH to 4.0 with dilute hydrochloric acid, slowly raise the temperature to 70°C, filter after reacting for 4 hours, and vacuum-dry to obtain expandable graphi...
PUM
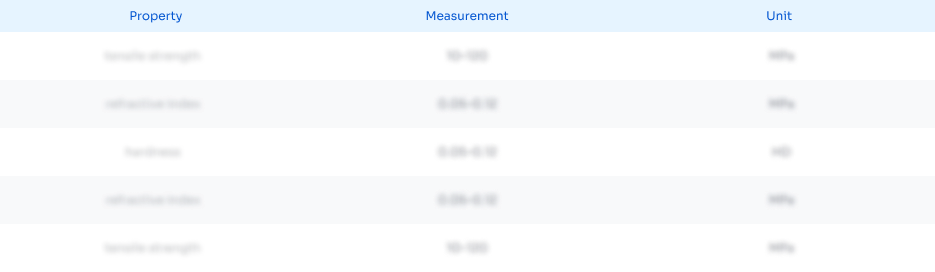
Abstract
Description
Claims
Application Information

- R&D Engineer
- R&D Manager
- IP Professional
- Industry Leading Data Capabilities
- Powerful AI technology
- Patent DNA Extraction
Browse by: Latest US Patents, China's latest patents, Technical Efficacy Thesaurus, Application Domain, Technology Topic, Popular Technical Reports.
© 2024 PatSnap. All rights reserved.Legal|Privacy policy|Modern Slavery Act Transparency Statement|Sitemap|About US| Contact US: help@patsnap.com