Friction stir welding method for aluminum alloy having changeable thickness
A technology of friction stir welding and welding method, which is applied in welding equipment, metal processing, non-electric welding equipment, etc., and can solve problems such as shortening of stirring needle length, affecting welding, and backing plate damage, so as to expand the application range, improve economic benefits, The effect of saving production cost
- Summary
- Abstract
- Description
- Claims
- Application Information
AI Technical Summary
Problems solved by technology
Method used
Image
Examples
Embodiment Construction
[0032] Now in conjunction with embodiment, accompanying drawing, the present invention will be further described:
[0033] figure 1 It is a schematic diagram of implementation of friction stir welding welding method for aluminum alloy sheets with variable thickness. After the laser measurement accuracy of the laser tracker 2 is calibrated by the distance in the height direction, it can measure the thickness of the aluminum alloy sheet in the forward direction of welding in real time, and feed back the measurement data to The numerical control system of the friction stir welding equipment, the numerical control system processes and analyzes the measurement data in real time, and the numerical control system drives the welding shaft in real time according to the feedback data, so as to realize the control of the penetration depth of the stirring needle 3 of the split stirring tool, and then realize the welding depth control to realize the friction stir welding of aluminum alloy ...
PUM
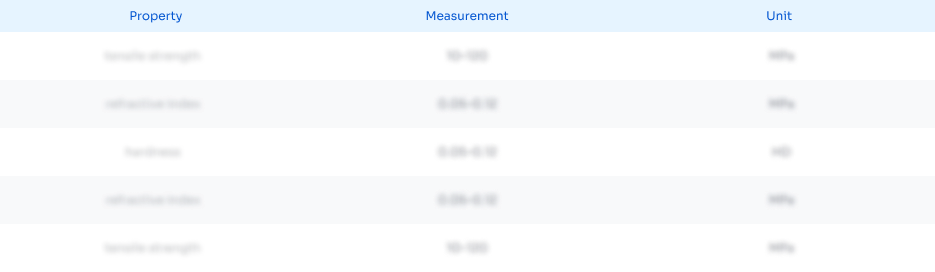
Abstract
Description
Claims
Application Information

- R&D Engineer
- R&D Manager
- IP Professional
- Industry Leading Data Capabilities
- Powerful AI technology
- Patent DNA Extraction
Browse by: Latest US Patents, China's latest patents, Technical Efficacy Thesaurus, Application Domain, Technology Topic, Popular Technical Reports.
© 2024 PatSnap. All rights reserved.Legal|Privacy policy|Modern Slavery Act Transparency Statement|Sitemap|About US| Contact US: help@patsnap.com